Audi UR Quattro Rally Build
#41

We made quite a lot of progress this week but it doesn’t feel like it. Perhaps because we didn’t get to actually bolt anything to the car. What we did do was finish prepping the transmission. We replaced the rear coupling and seals with a non-broken version, cleaned and painted the case, installed new drain and fill plugs, replaced the input shaft seal and installed the mounts and brackets. Mounts are 034 Motorsport in Delrin.


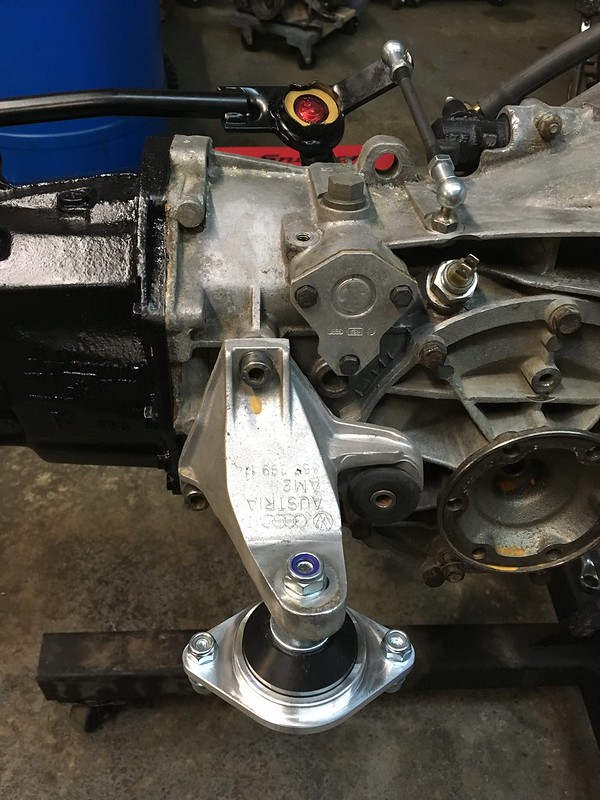

People keep telling us we really need to run with the big, heavy rubber damper mounted to the back of the transmission as Audi intended but we’d really rather leave it off. Are we nuts?
We also managed to recommission our ancient, homebuilt sand blaster and put it to work on some rusty components. Unfortunately, in our excited state, we forgot to take the “before” pictures.
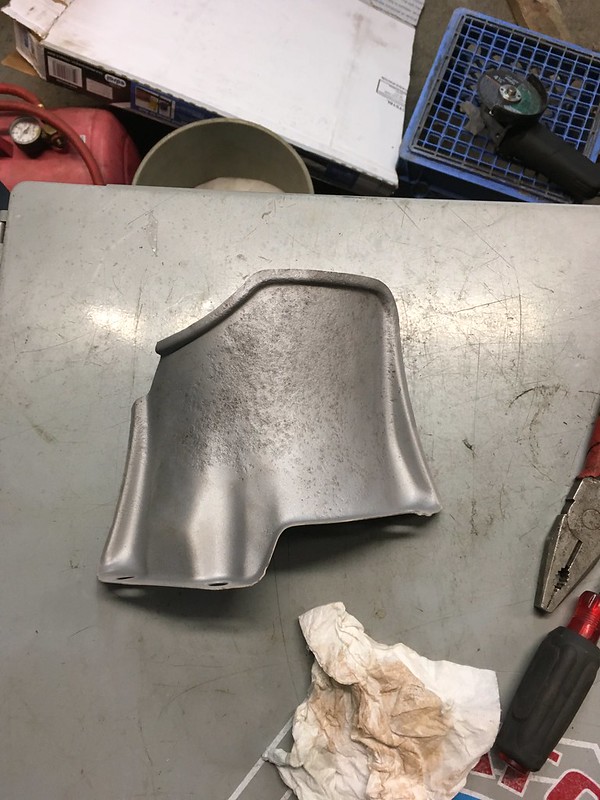
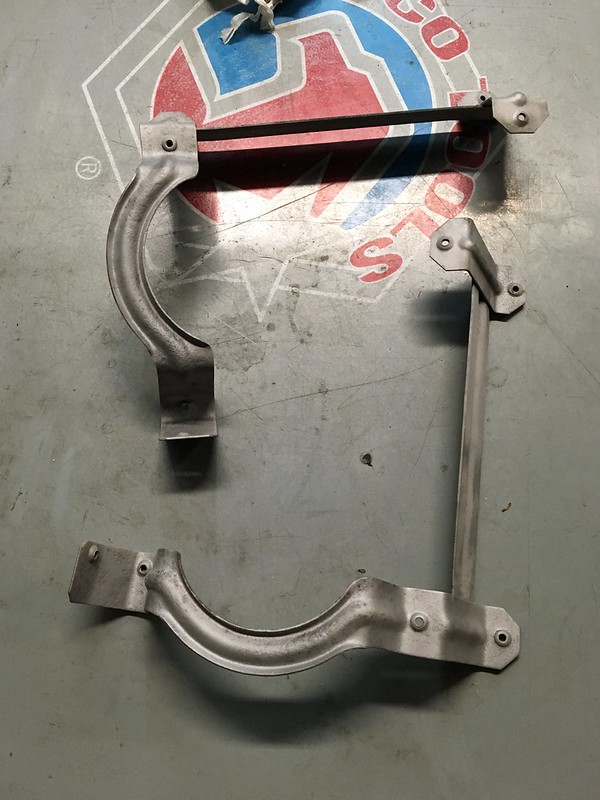
Next week we hope to modify the dash to fit over the steering column and get some parts plated. We will also look for something to bolt to the car. Exciting!!!!!!!


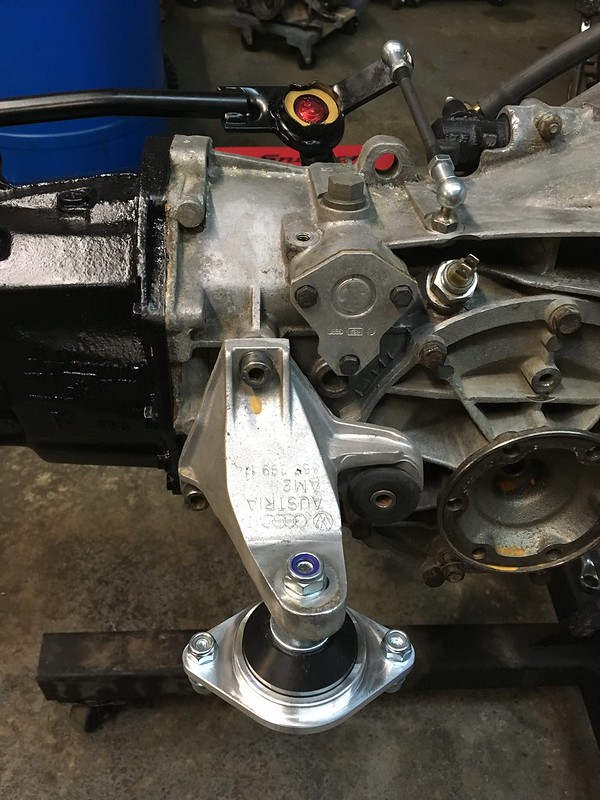

People keep telling us we really need to run with the big, heavy rubber damper mounted to the back of the transmission as Audi intended but we’d really rather leave it off. Are we nuts?
We also managed to recommission our ancient, homebuilt sand blaster and put it to work on some rusty components. Unfortunately, in our excited state, we forgot to take the “before” pictures.
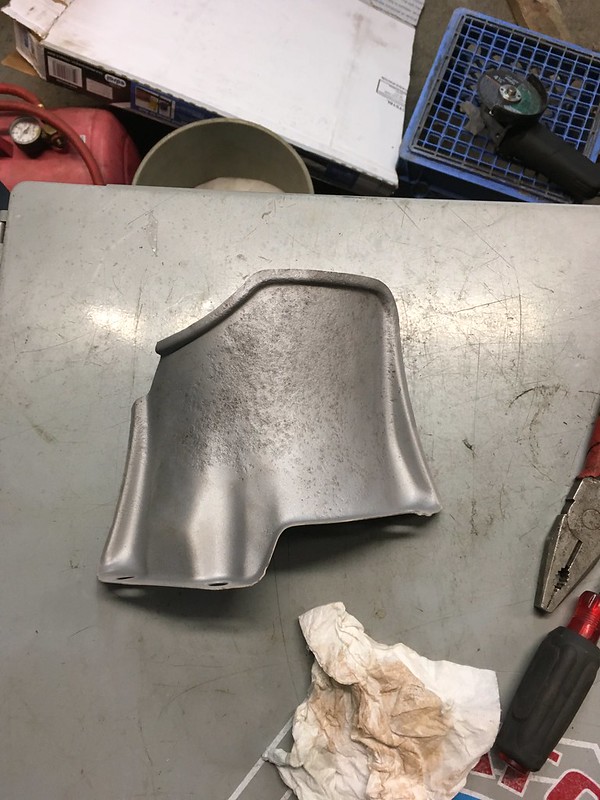
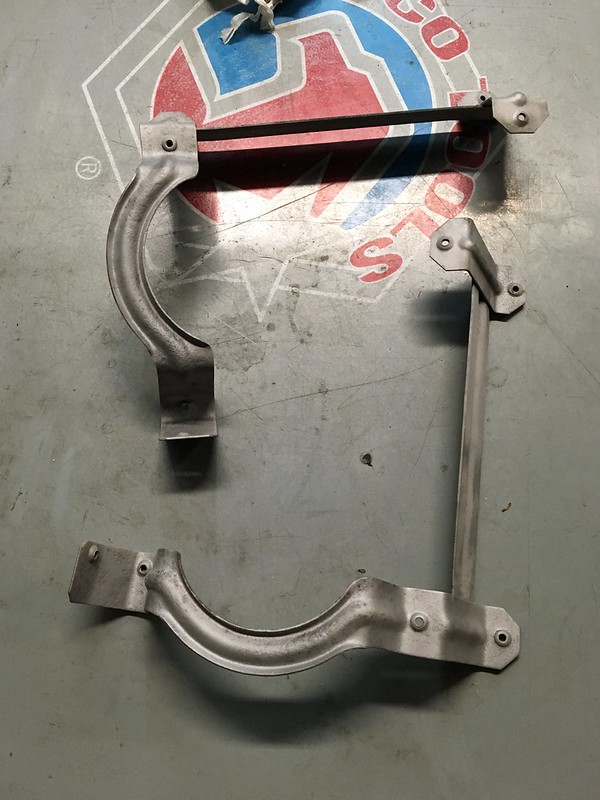
Next week we hope to modify the dash to fit over the steering column and get some parts plated. We will also look for something to bolt to the car. Exciting!!!!!!!
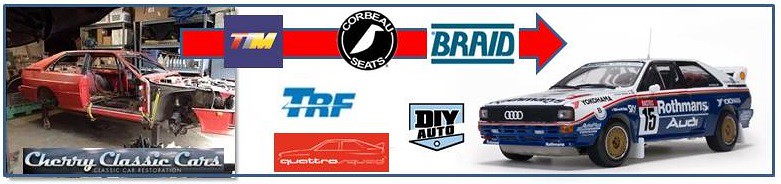
#42

Like most car nuts we are easily distracted by shiny things that come in the mail. This week was particularly distracting in that regard:
Clutch bulkhead brace from 034 Motorsports:
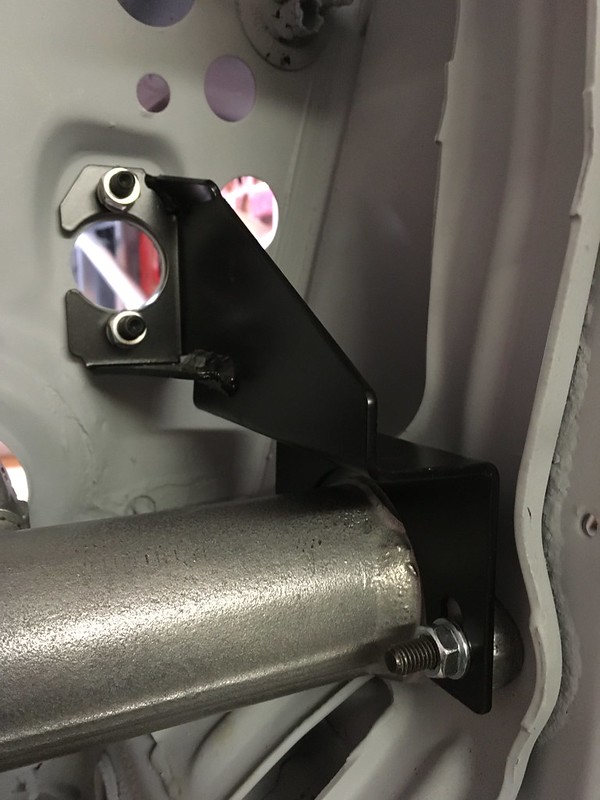
Solid Delrin engine mounts from 034 Motorsports:
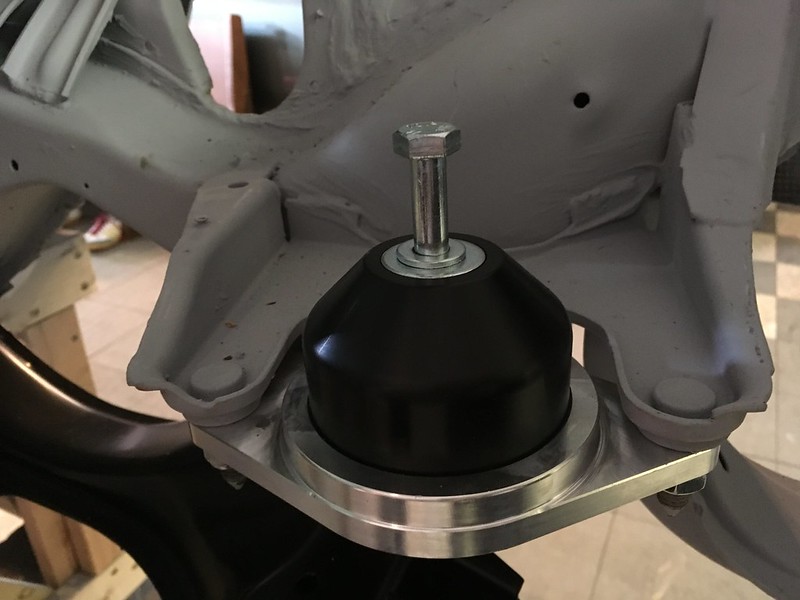
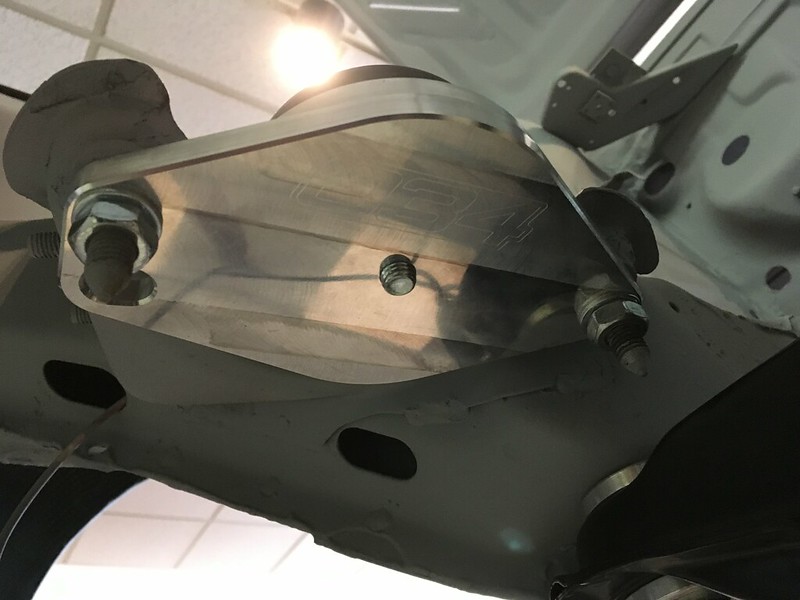
Transmission mounts from 034 Motorsports:

[/url]
Short shift kit from 034 Motorsport (of course):

We also gave the car its own "woom" to gestate in. Do you think it will be ready in nine months?
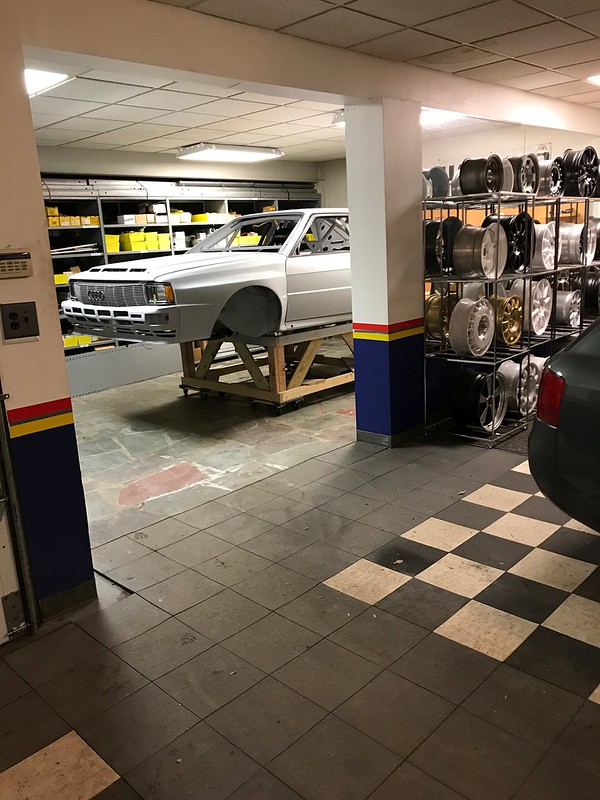
Next up. Hacking up the dash to make it fit.
Clutch bulkhead brace from 034 Motorsports:
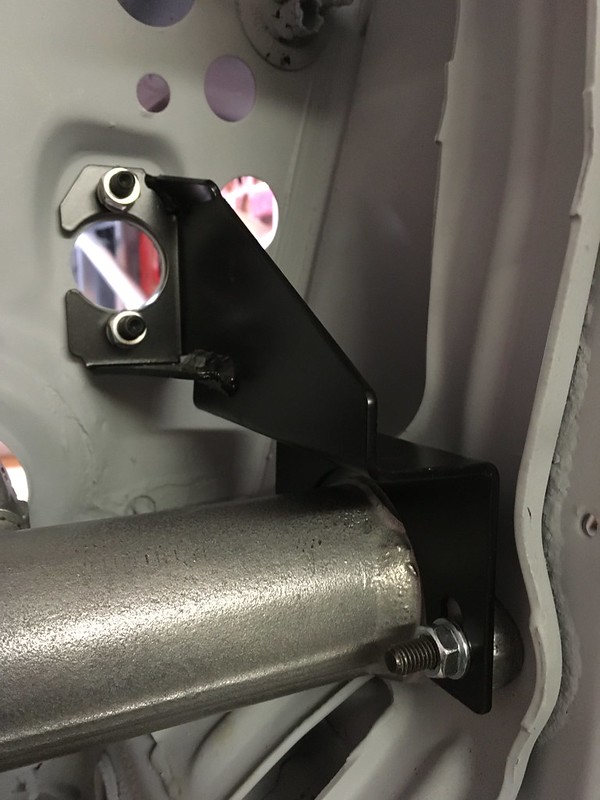
Solid Delrin engine mounts from 034 Motorsports:
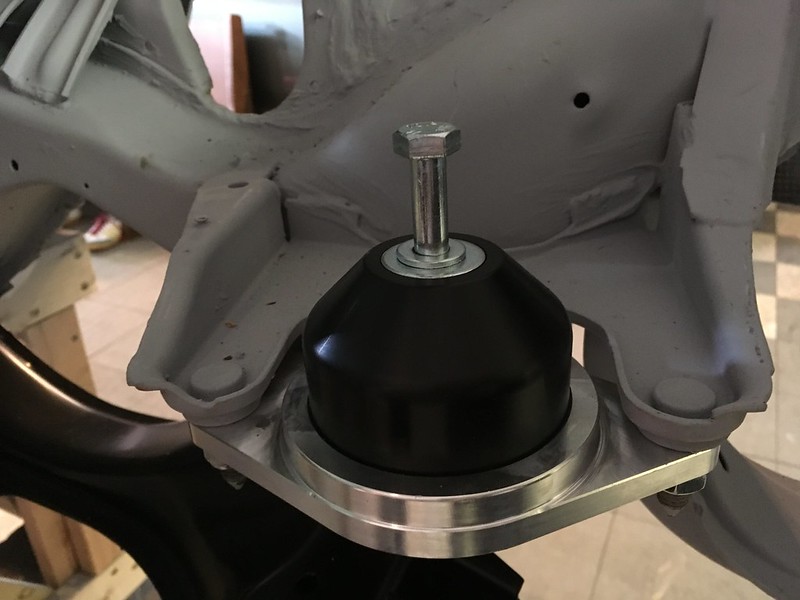
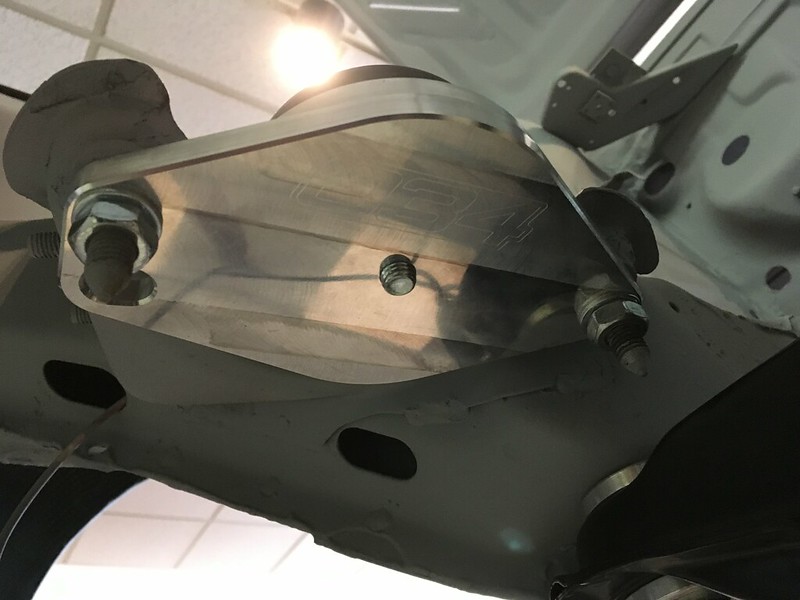
Transmission mounts from 034 Motorsports:


Short shift kit from 034 Motorsport (of course):

We also gave the car its own "woom" to gestate in. Do you think it will be ready in nine months?
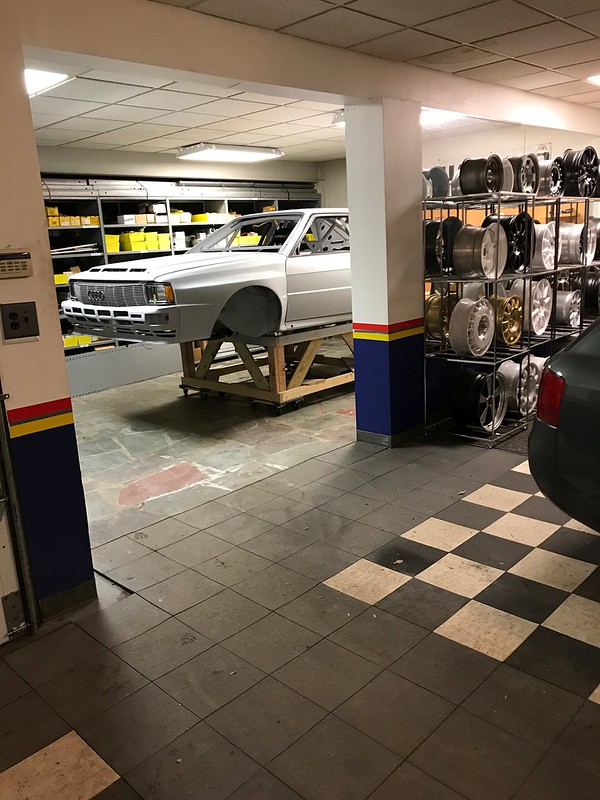
Next up. Hacking up the dash to make it fit.
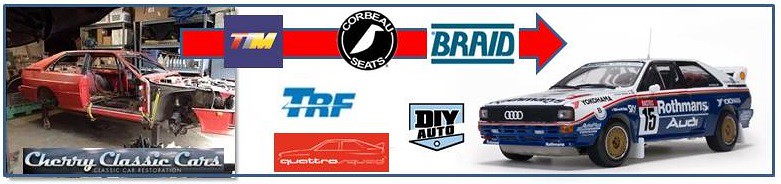
#43

It’s time to make the Group B rally dash actually fit in the car. This is a reproduction panel modelled on an original by a member of the US Quattro community and is beautifully crafted. Unfortutunately they have to be “relieved” to fit round the steering column as the lower return is supplied straight. You can’t just cut it as it would then be too flimsy. An added complication is that we intend to still use the ignition key so we have to make room for the barrel housing too. You can see the interference here:
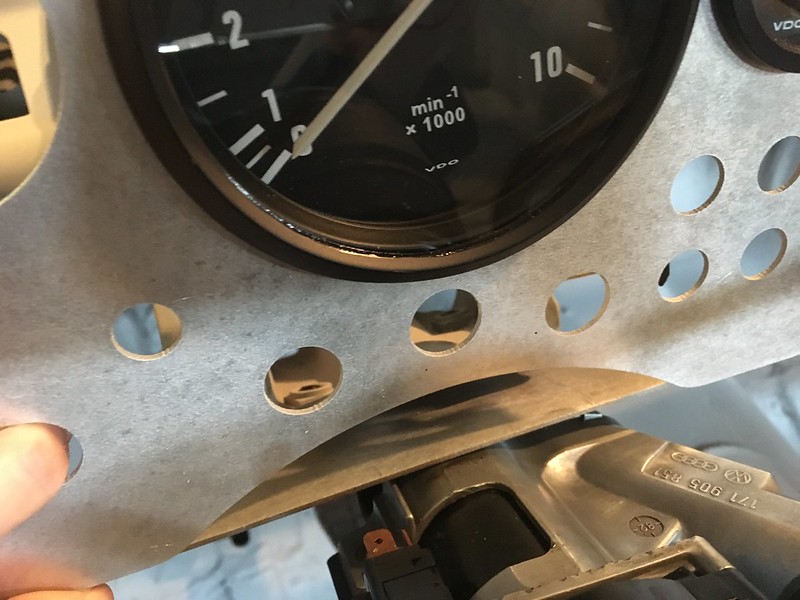

That bottom flange needs to follow the curvature of the panel. To do so it needs to be cut, formed and then a bridge piece added to maintain its rigidity. Then we will need to remove some material to clear the lock. We will have to do all this with the gauge panel in place or it will easily distort.


These fasteners will be replaced with rivets once we are confident everything fits.

Then we needed to clear the ignition key housing:


The dash panel is suspended from the dash bar welded between the cage A pillar bars but will need some bracing beneath to stop it swinging back and forth. We fabricated these brackets and used the holes from the old cage to help mount them.
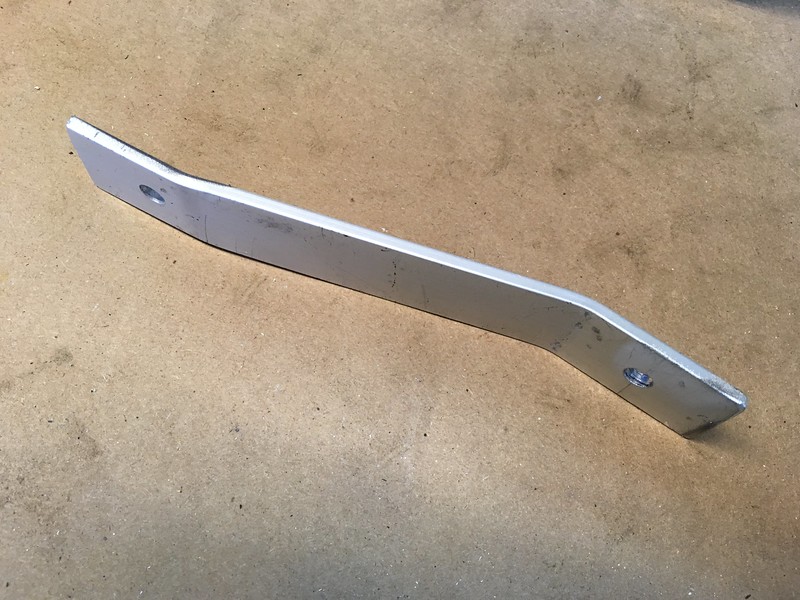
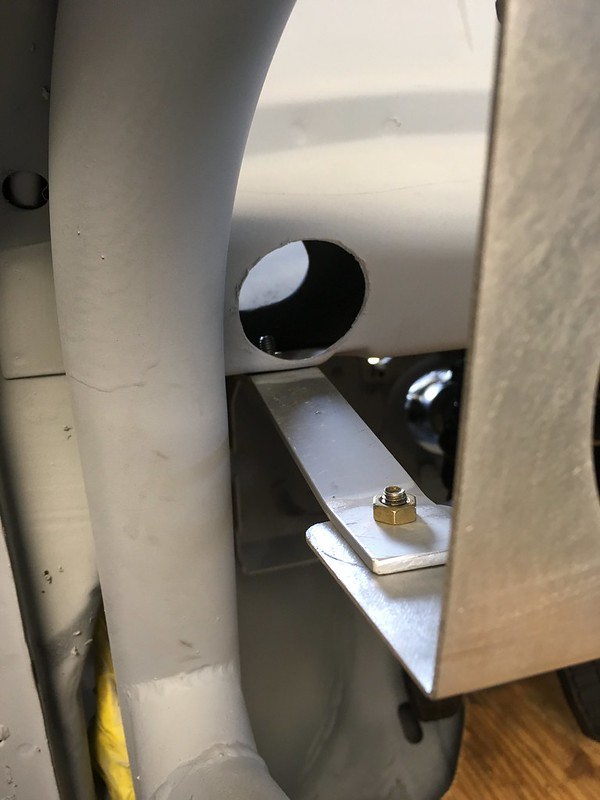
Done!
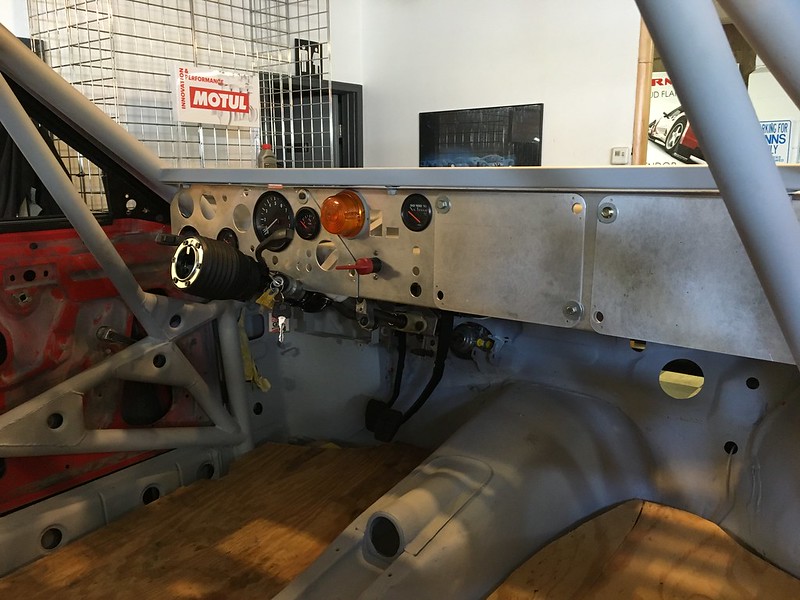
Now to mount some more gauges, fuses and a computer!

(These are just a small selection of the pictures we have taken. You can see all of them at https://flic.kr/s/aHskqskKvZ)
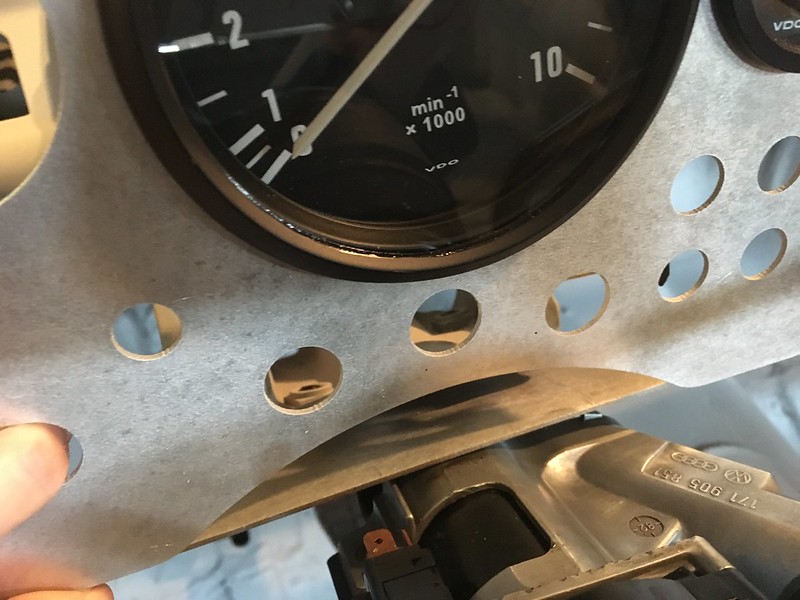

That bottom flange needs to follow the curvature of the panel. To do so it needs to be cut, formed and then a bridge piece added to maintain its rigidity. Then we will need to remove some material to clear the lock. We will have to do all this with the gauge panel in place or it will easily distort.


These fasteners will be replaced with rivets once we are confident everything fits.

Then we needed to clear the ignition key housing:


The dash panel is suspended from the dash bar welded between the cage A pillar bars but will need some bracing beneath to stop it swinging back and forth. We fabricated these brackets and used the holes from the old cage to help mount them.
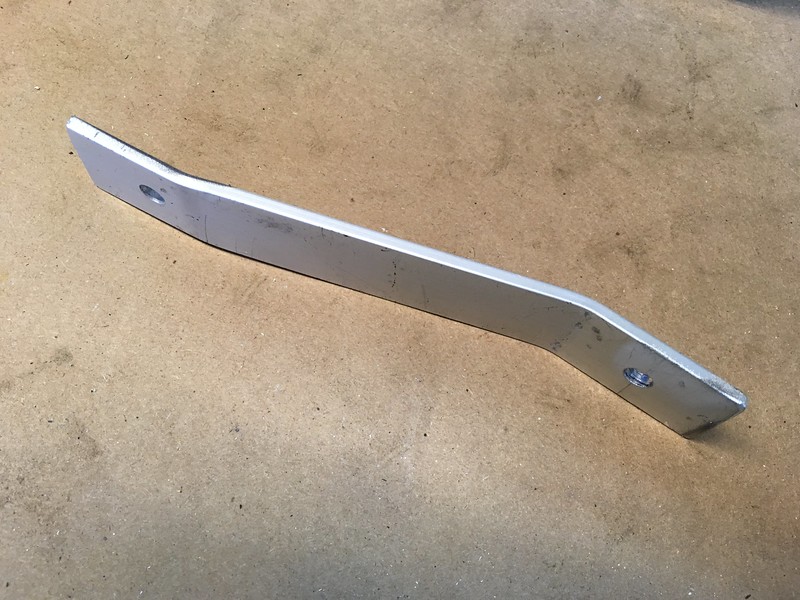
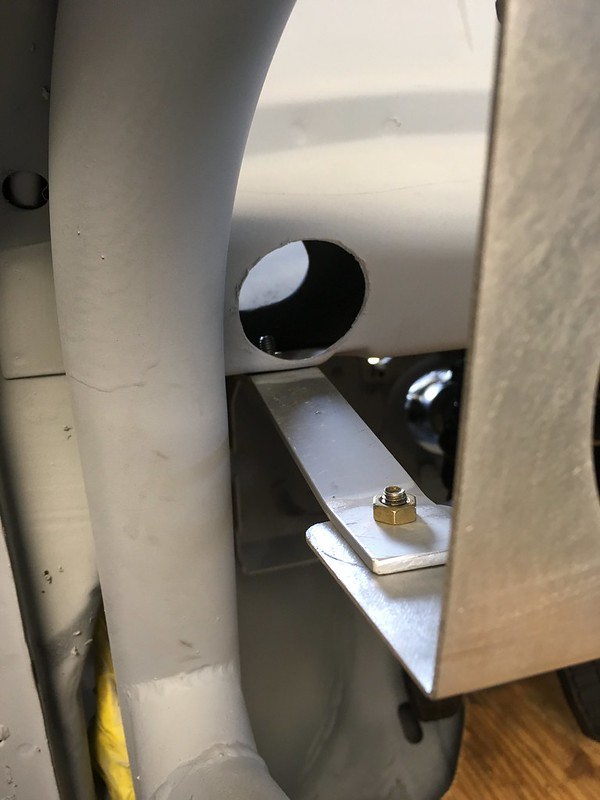
Done!
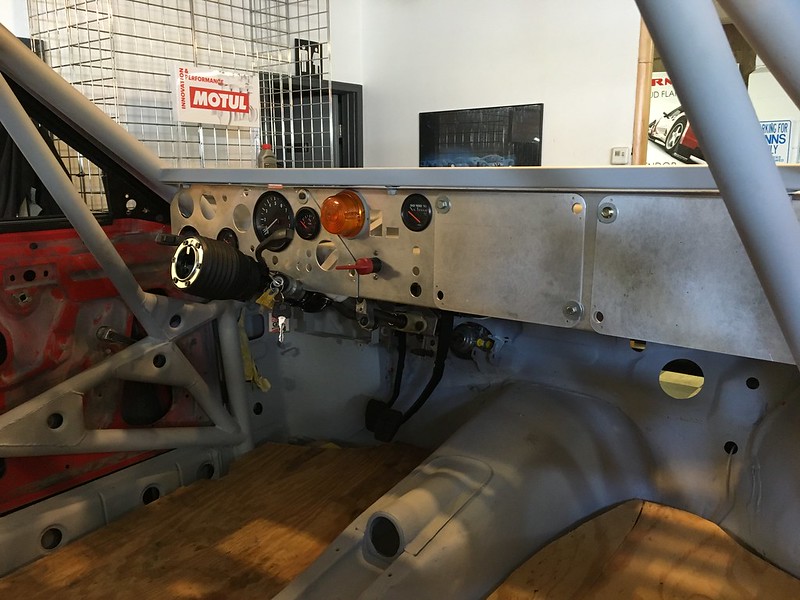
Now to mount some more gauges, fuses and a computer!

(These are just a small selection of the pictures we have taken. You can see all of them at https://flic.kr/s/aHskqskKvZ)
#44

The dash on the Group B Quattros is somewhat iconic especially the big orange oil light in the middle. For this reason we have been very keen to progress work in this area.
Our large tachometer came without any mounting hardware. It looks like it was designed to mount into a rubber grommet like the Porsche 911 gauges. That was never going to work with the 2mm thick aluminium dash we are working with so we had to get creative. First we tried a large hose clamp but of course it rattled around.

Then we butchered some garage door seal for its rubber and tried that under the hose clamp.


This worked as the clamp squeezed itself up against the back of the dash but didn’t really look the part. We found a roll of thicker black seal in the back of the shop and sliced that up instead. Success!
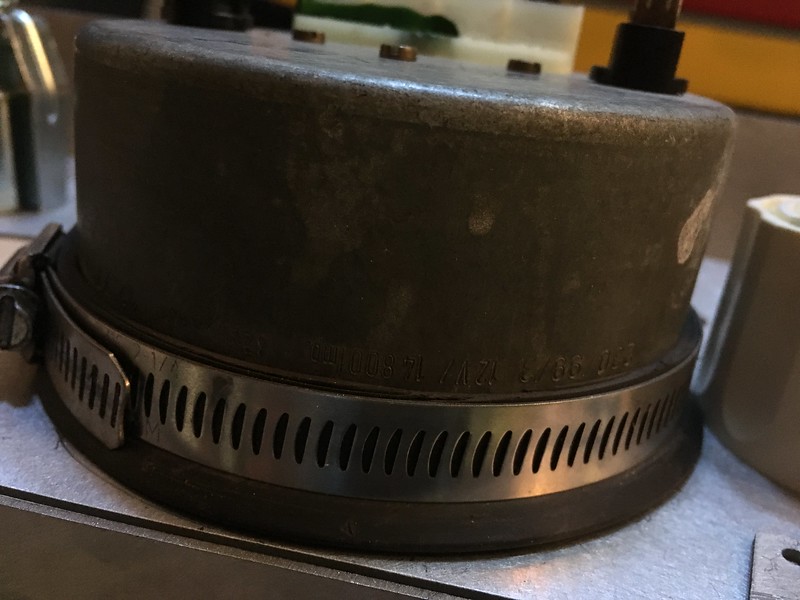
Then our missing VDO gauges came in from egauges.com so we mounted them up. The threaded sleeve on these makes installation so much easier than the yoke and thumb nuts of old.
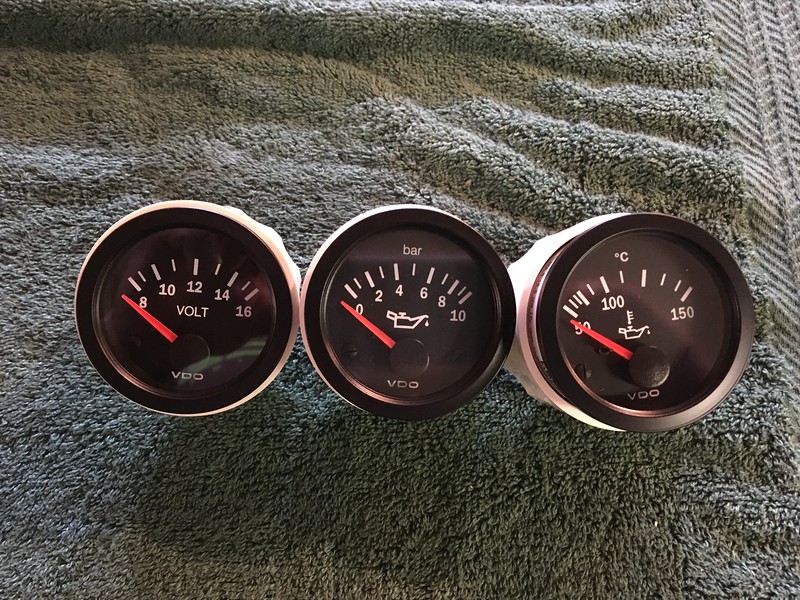
Our tachometer came without mounting studs but no yoke so we made one.
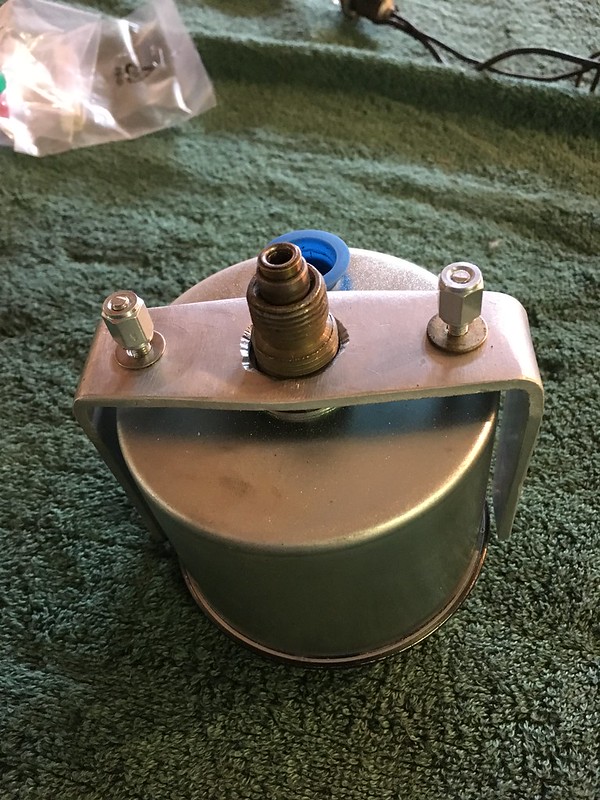
Then we just had to put it into the car.
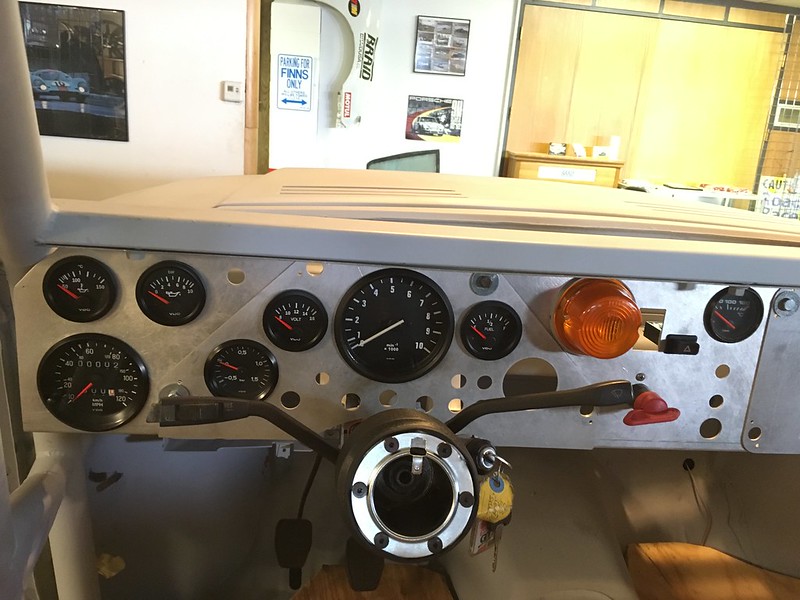
All it needs now is warning lights and switches, mostly.
We were also very excited to receive a box of metric flange nuts and bolts we found on eBay. These will be very useful.
Yes, we know, we’re nuts!
Our large tachometer came without any mounting hardware. It looks like it was designed to mount into a rubber grommet like the Porsche 911 gauges. That was never going to work with the 2mm thick aluminium dash we are working with so we had to get creative. First we tried a large hose clamp but of course it rattled around.

Then we butchered some garage door seal for its rubber and tried that under the hose clamp.


This worked as the clamp squeezed itself up against the back of the dash but didn’t really look the part. We found a roll of thicker black seal in the back of the shop and sliced that up instead. Success!
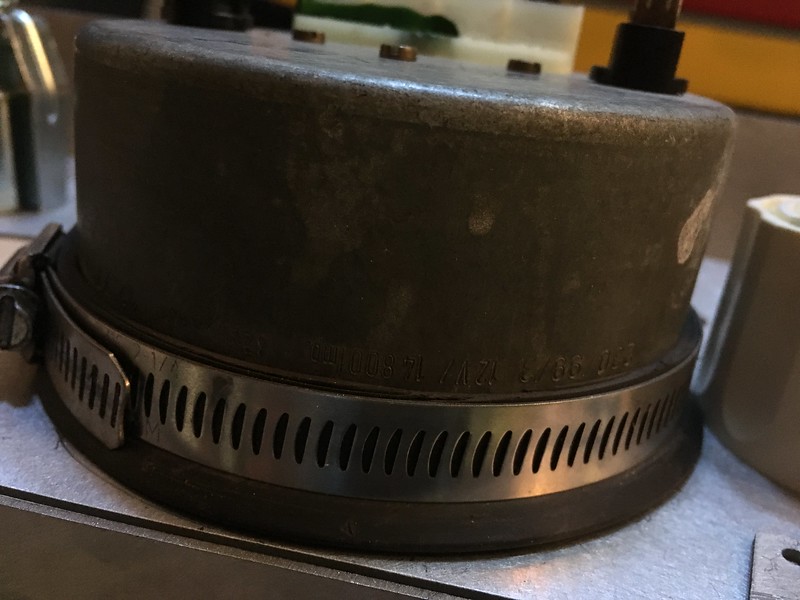
Then our missing VDO gauges came in from egauges.com so we mounted them up. The threaded sleeve on these makes installation so much easier than the yoke and thumb nuts of old.
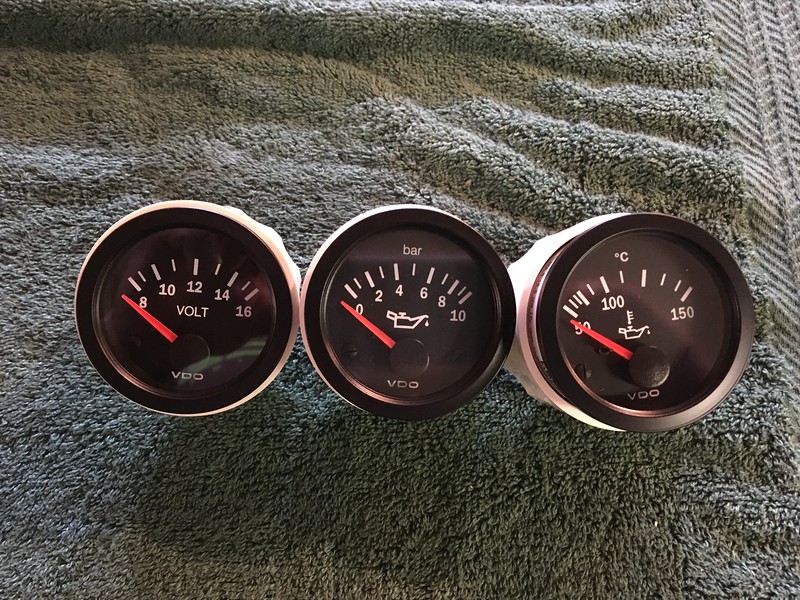
Our tachometer came without mounting studs but no yoke so we made one.
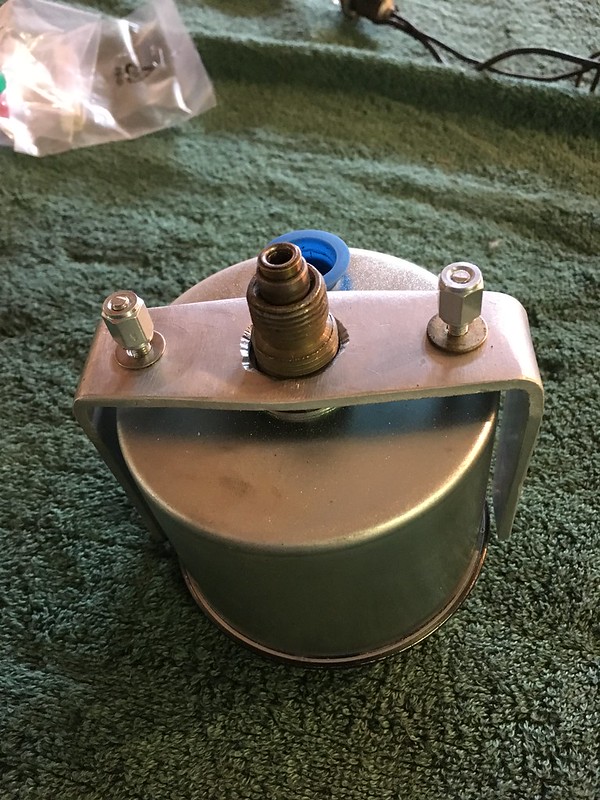
Then we just had to put it into the car.
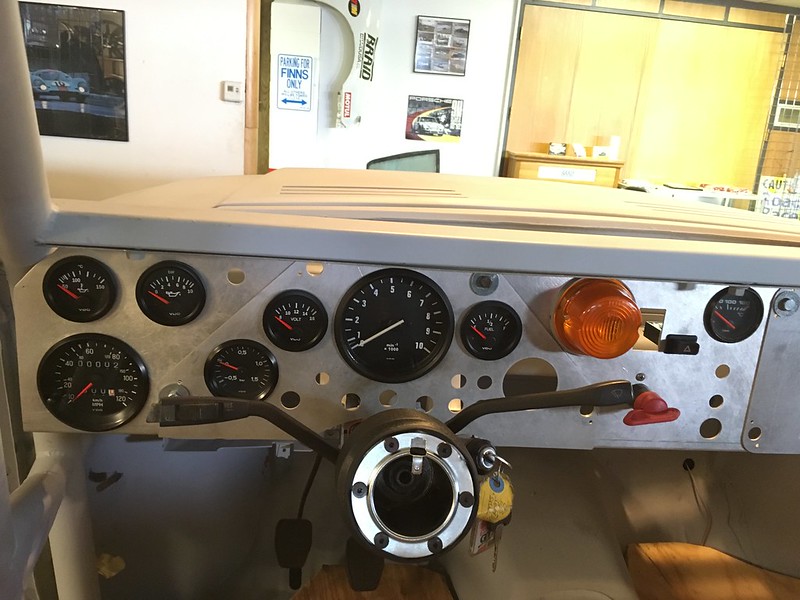
All it needs now is warning lights and switches, mostly.
We were also very excited to receive a box of metric flange nuts and bolts we found on eBay. These will be very useful.

Yes, we know, we’re nuts!
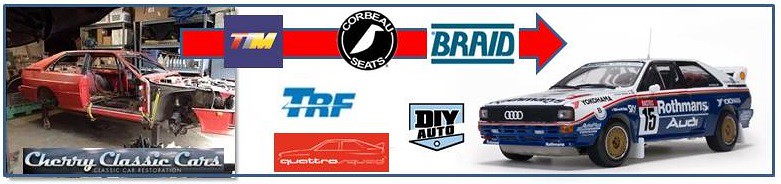
#45

We took our first foray into replating components recently. Many steel components on 80s German cars have a gold finish which was at the time probably cadmium plating. These days, due to EPA regulations, zinc dichromate plating seems to be a better option. You can do it in-house quite easily but the dichromate part is really toxic so we prefer to have it done as far away from our shop as practicable. We have also resisted the temptation to lick the newly finished parts.
First step in the process is to degrease the components and then to remove all the rust by blasting. As we mentioned earlier, we recently recommissioned our home-made sand blaster so used that to blast a bunch of accumulated parts.
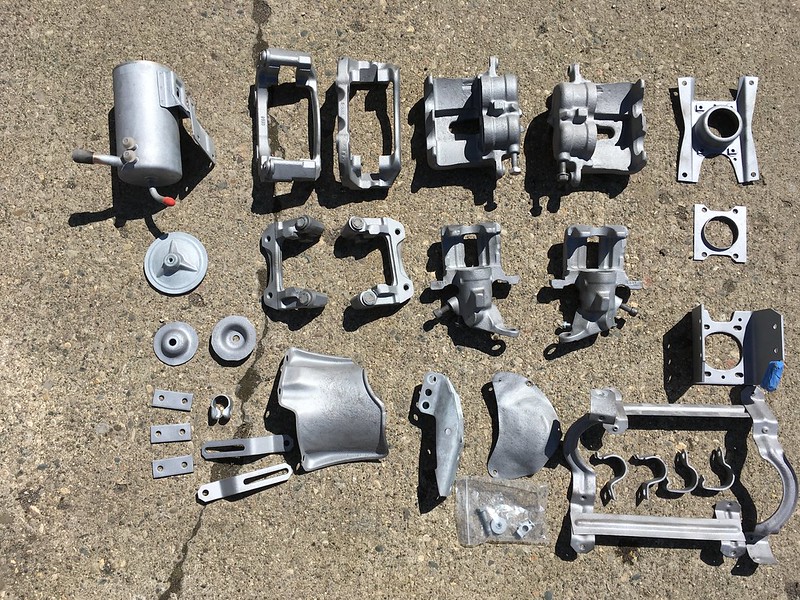
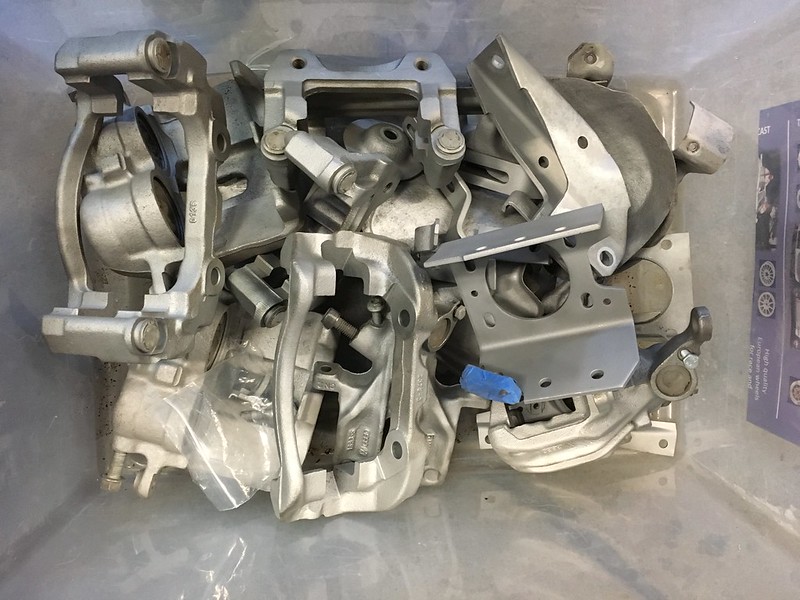
We boxed them up and ran them over to Plating Specialists Inc. in Madison Heights. A safe 15 miles from our shop. Two weeks and $240 later WOW:
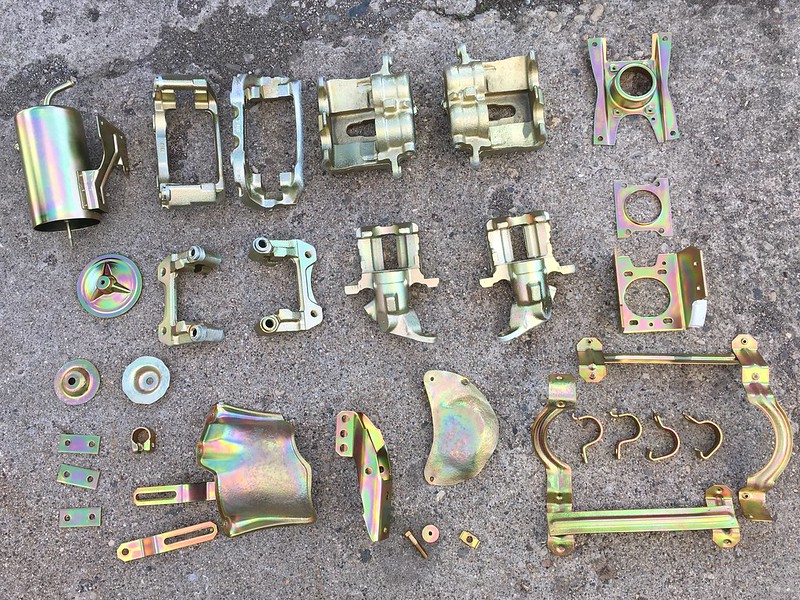
We couldn’t help but bolt a few components to the car:
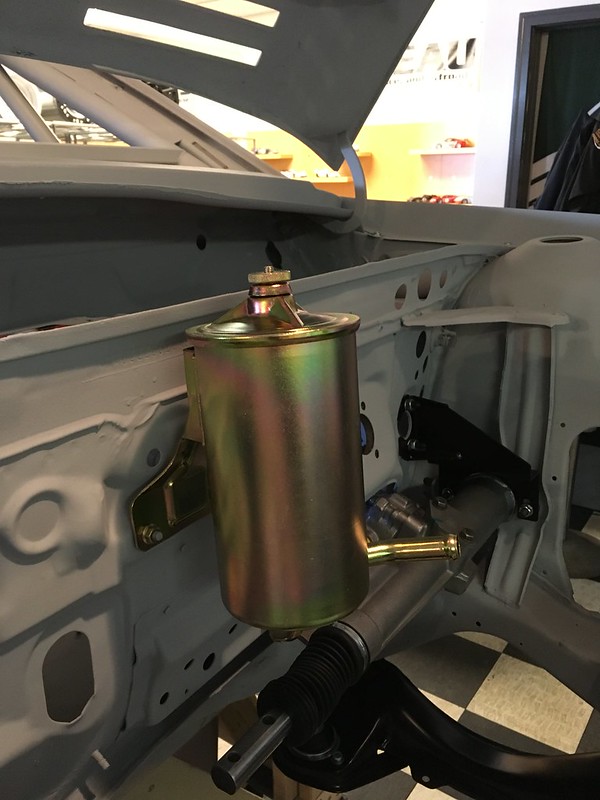
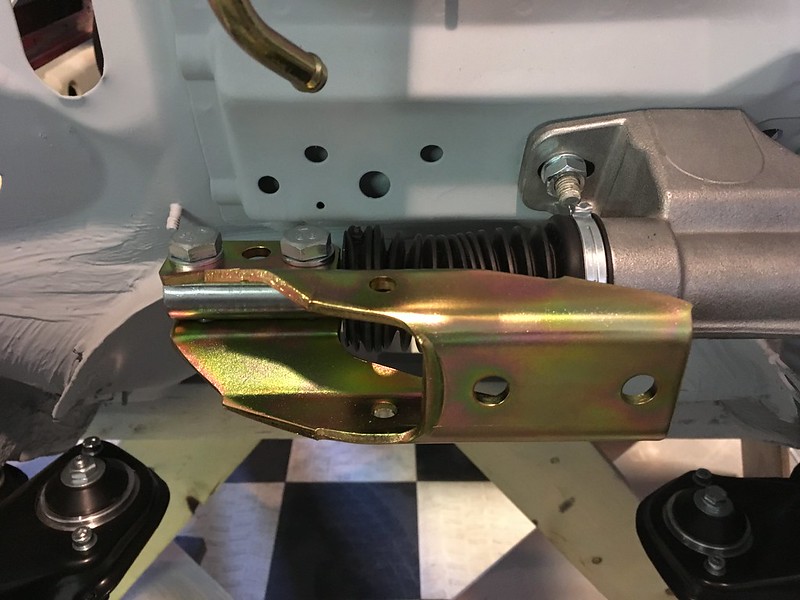
We think we might be addicted to zinc dichromate plating now.
First step in the process is to degrease the components and then to remove all the rust by blasting. As we mentioned earlier, we recently recommissioned our home-made sand blaster so used that to blast a bunch of accumulated parts.
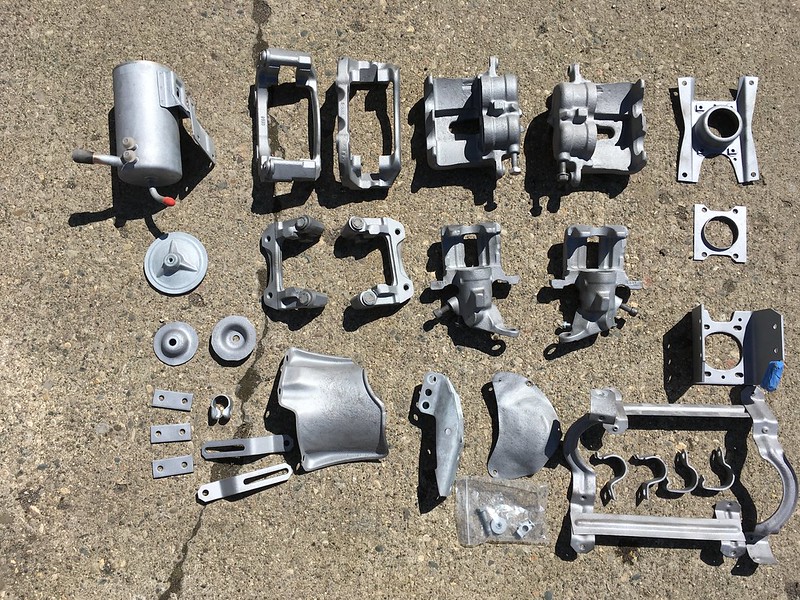
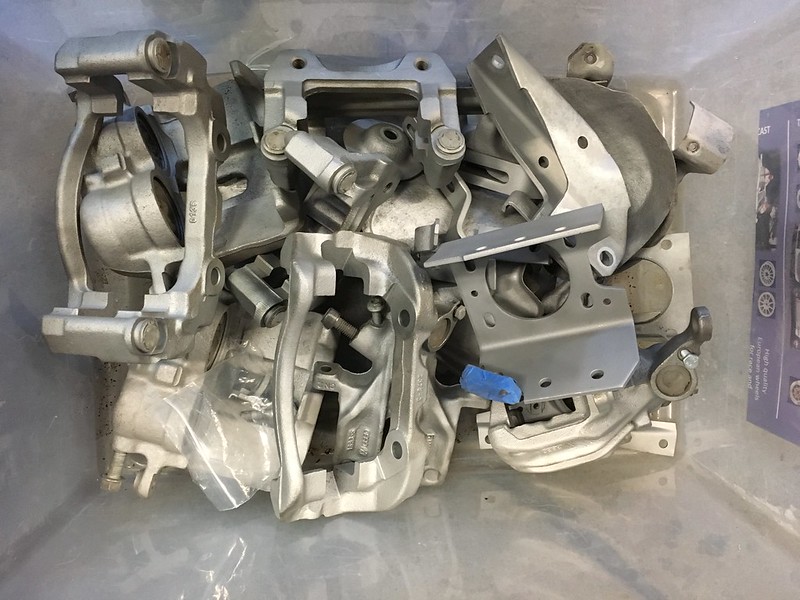
We boxed them up and ran them over to Plating Specialists Inc. in Madison Heights. A safe 15 miles from our shop. Two weeks and $240 later WOW:
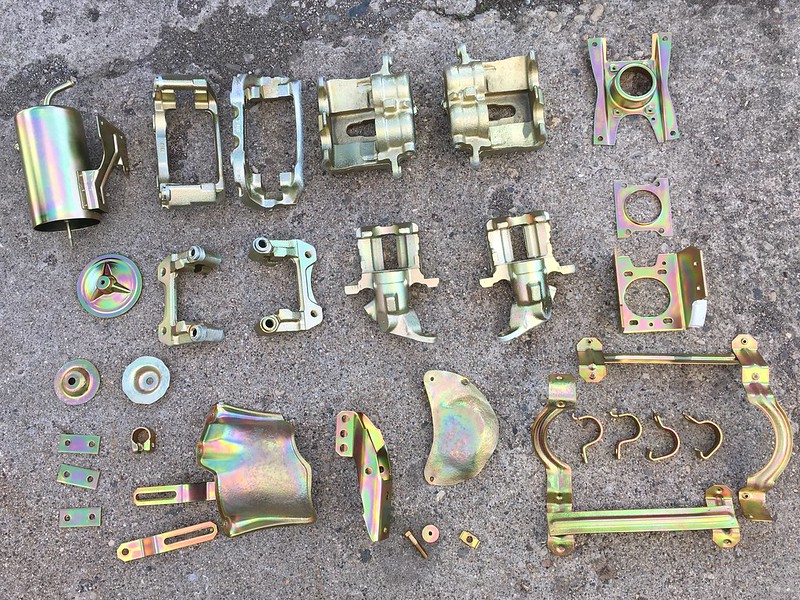
We couldn’t help but bolt a few components to the car:
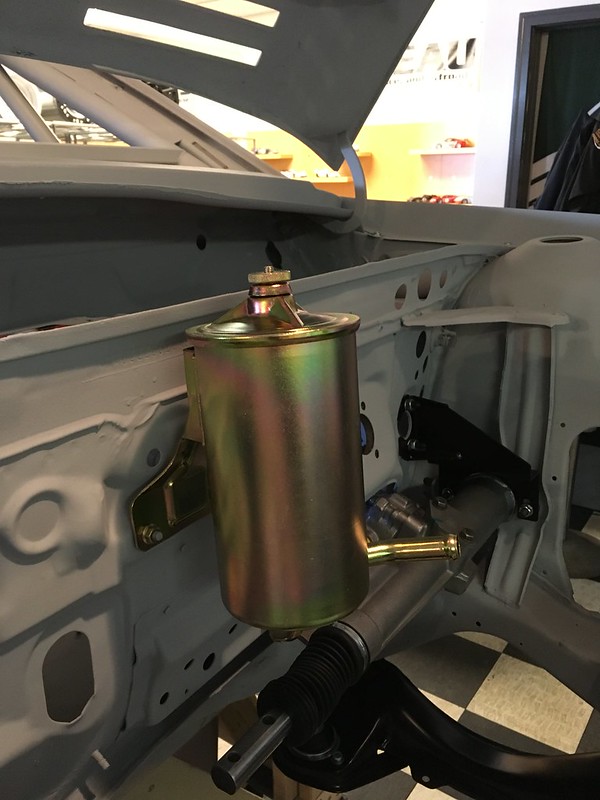
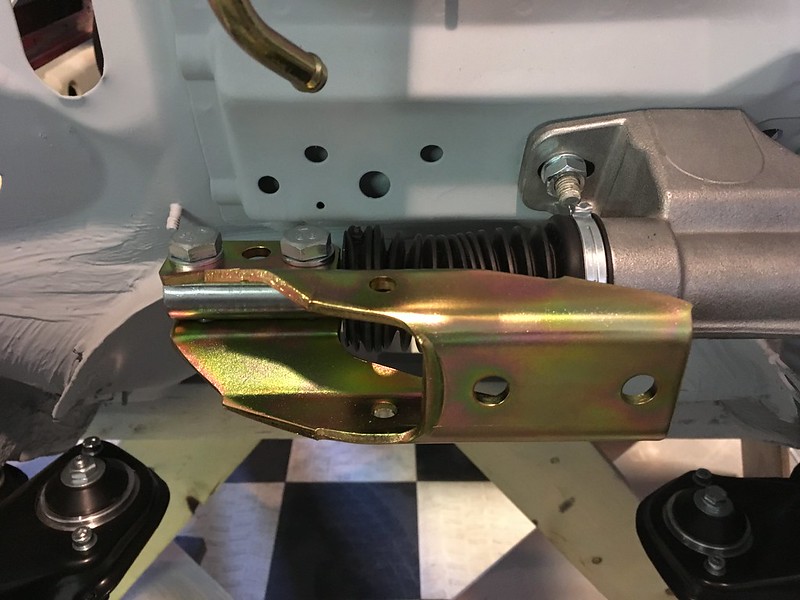
We think we might be addicted to zinc dichromate plating now.
#46

SHORT SHIFTER
We mentioned earlier that we had purchased a short shift kit from 034 Motorsports. Well, with our freshly plated shifter components back at the shop we wasted no time in assembling it and bolting it in. This is the stock shifter:
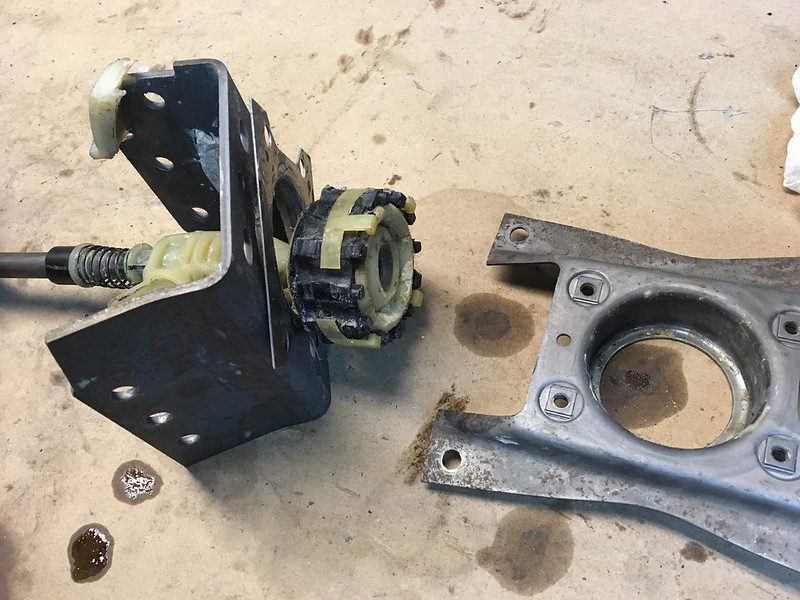
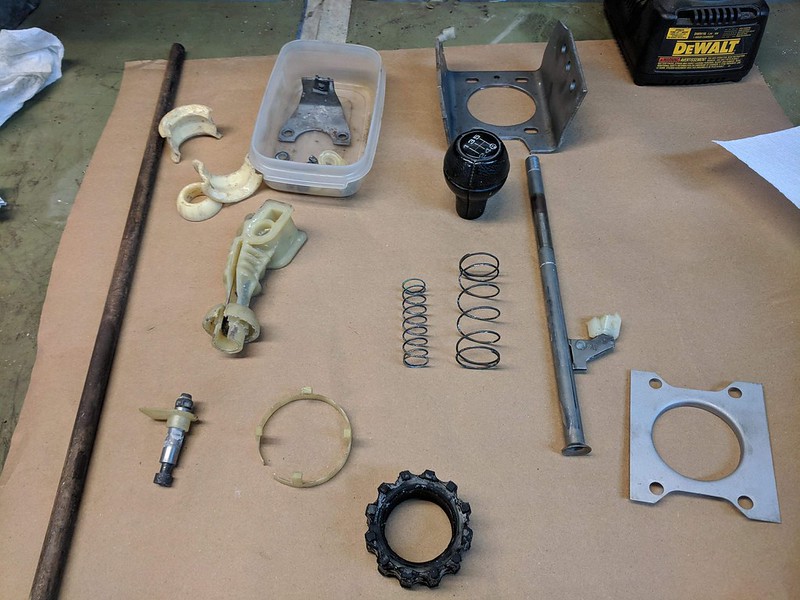
And the freshly plated components and short shift kit jigsaw puzzle:
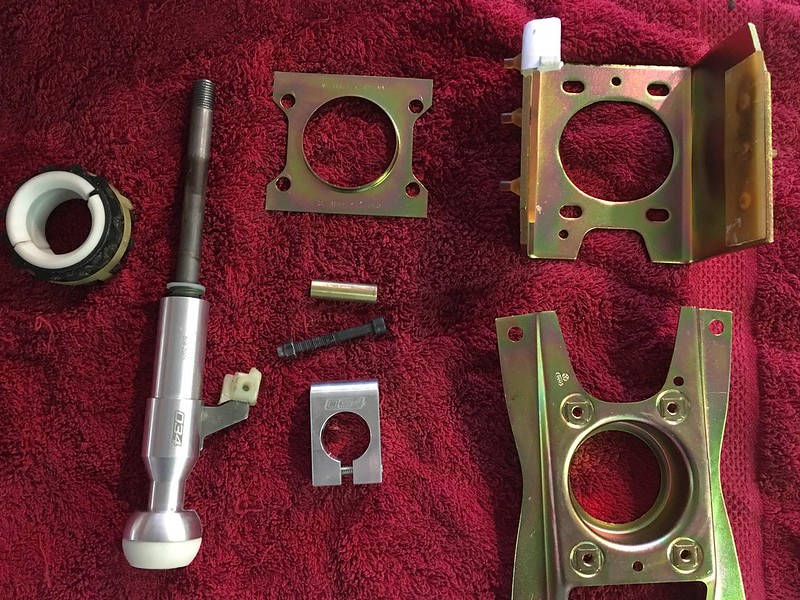
We soon had it together:

And bolted in the car:

Of course the transmission is not in so the shift rod is just hanging in space for now.
GAS PEDAL
During or shifter assembling we stumbled upon the gas pedal. We knew it couldn’t evade us forever. The pivot bushings seemed fine so we quickly slapped it in the car and made VROOM - VROOM noises.
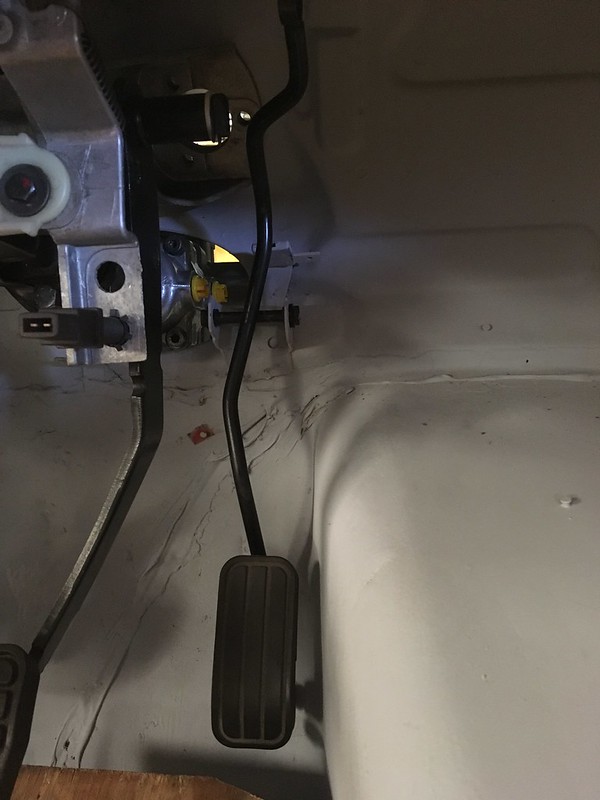
We are not sure if we are going to employ the original method of connecting the accelerator cable though. Seems a bit weird.
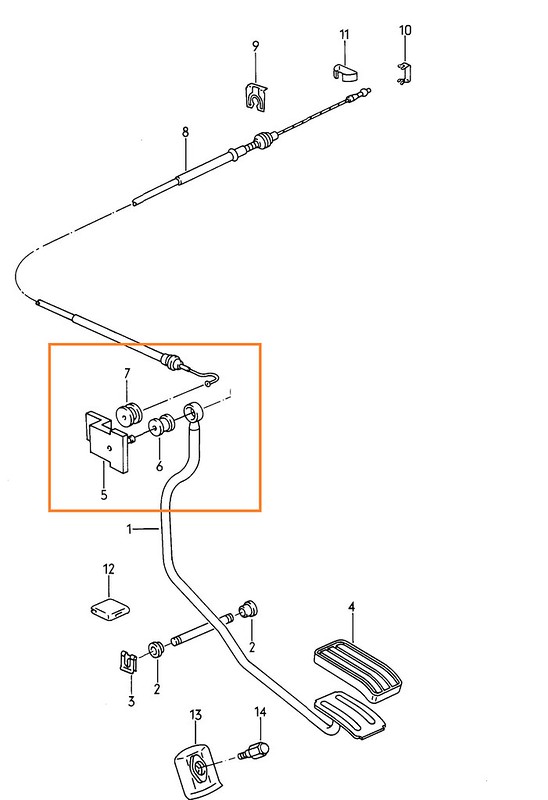
After all that hard work we felt we deserved a sit down and a nice cup of tea:

We mentioned earlier that we had purchased a short shift kit from 034 Motorsports. Well, with our freshly plated shifter components back at the shop we wasted no time in assembling it and bolting it in. This is the stock shifter:
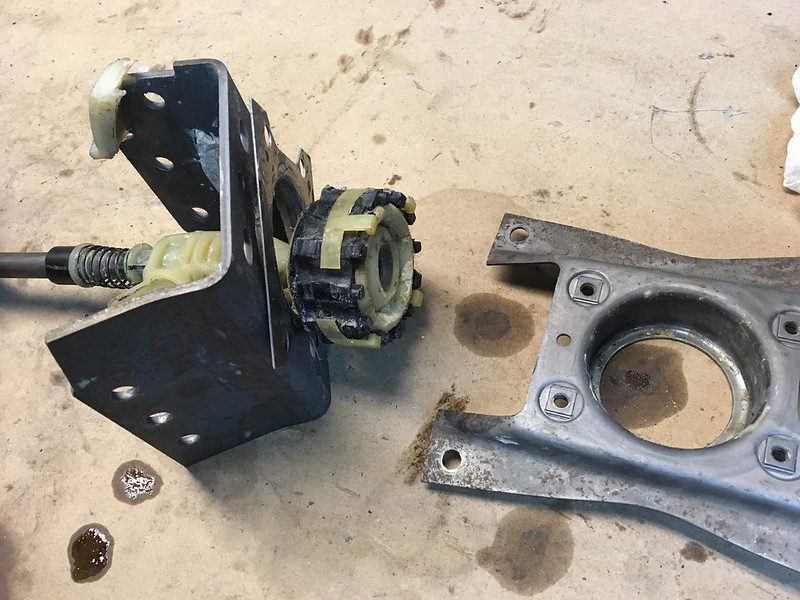
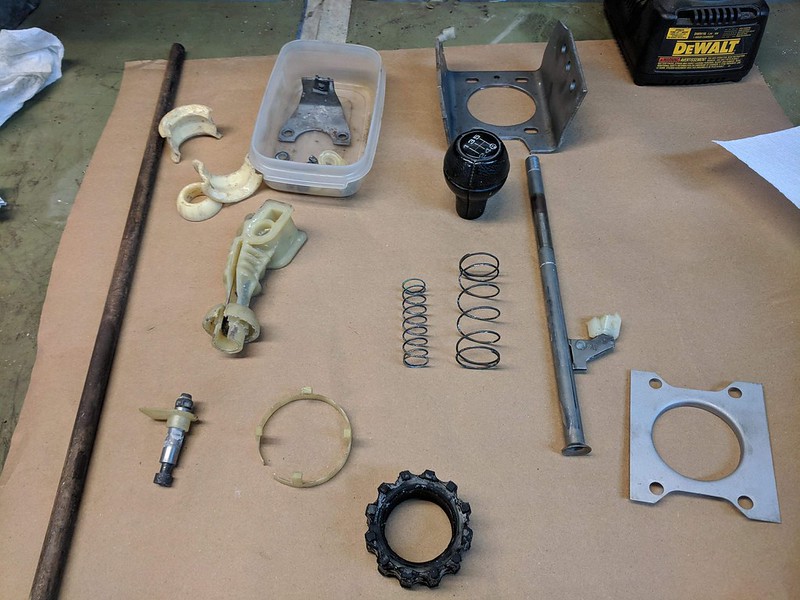
And the freshly plated components and short shift kit jigsaw puzzle:
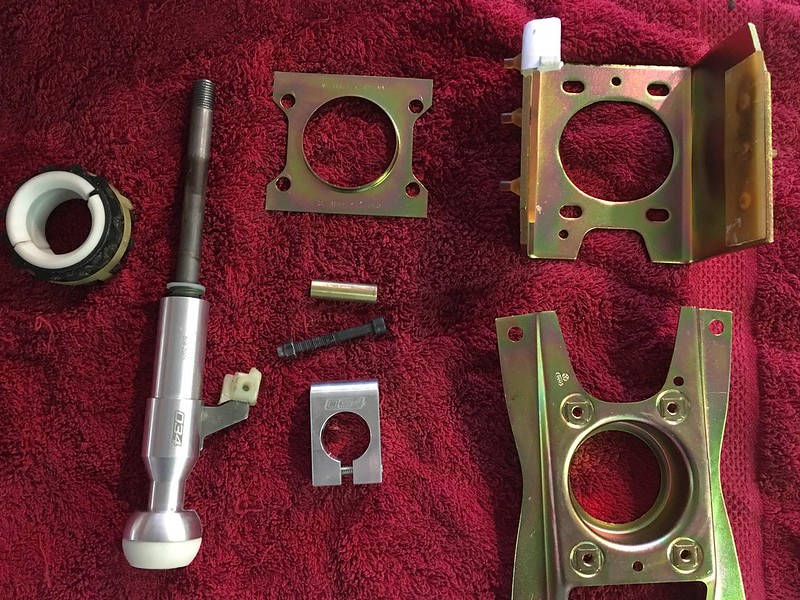
We soon had it together:

And bolted in the car:

Of course the transmission is not in so the shift rod is just hanging in space for now.
GAS PEDAL
During or shifter assembling we stumbled upon the gas pedal. We knew it couldn’t evade us forever. The pivot bushings seemed fine so we quickly slapped it in the car and made VROOM - VROOM noises.
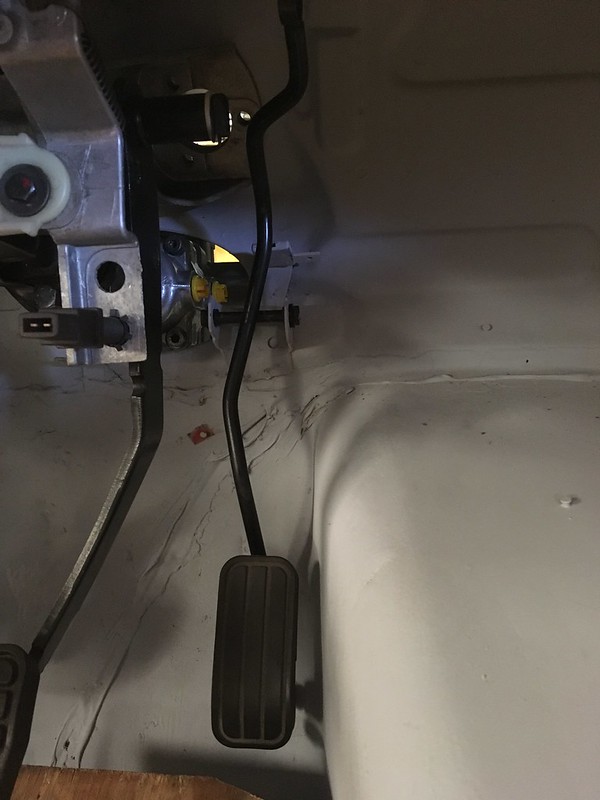
We are not sure if we are going to employ the original method of connecting the accelerator cable though. Seems a bit weird.
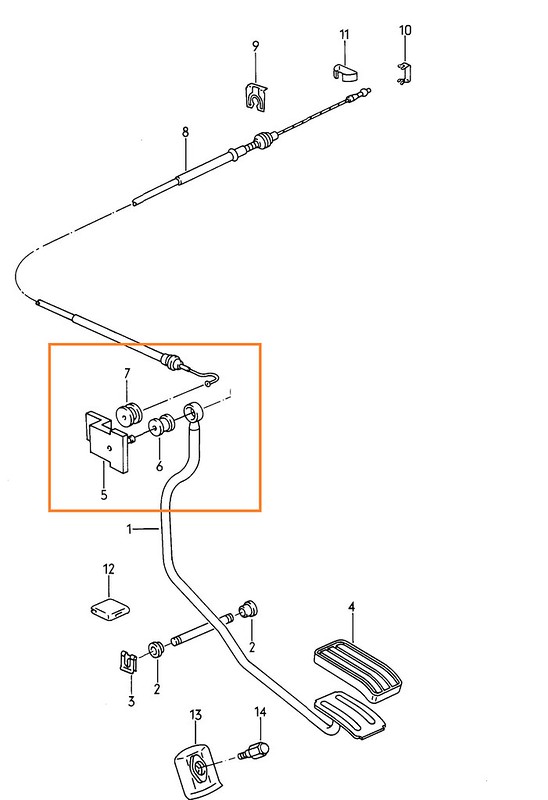
After all that hard work we felt we deserved a sit down and a nice cup of tea:

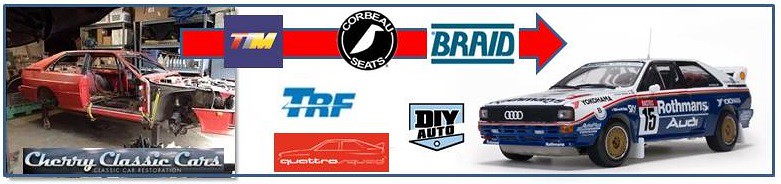
#47

It’s been a while since we got to work on the rally Quattro project so also a while since any updates. We have been distracted by other projects such as getting our 85 Quattro ready for the Concours D’elegance of America towards the end of July. Happily the car won an award so it was worth the effort.

As you may recall the car came with some suspension parts, the origin of which we could not determine. Namely: delrin control arm bushings, coil-over conversion kit and spherical bearing top mounts.

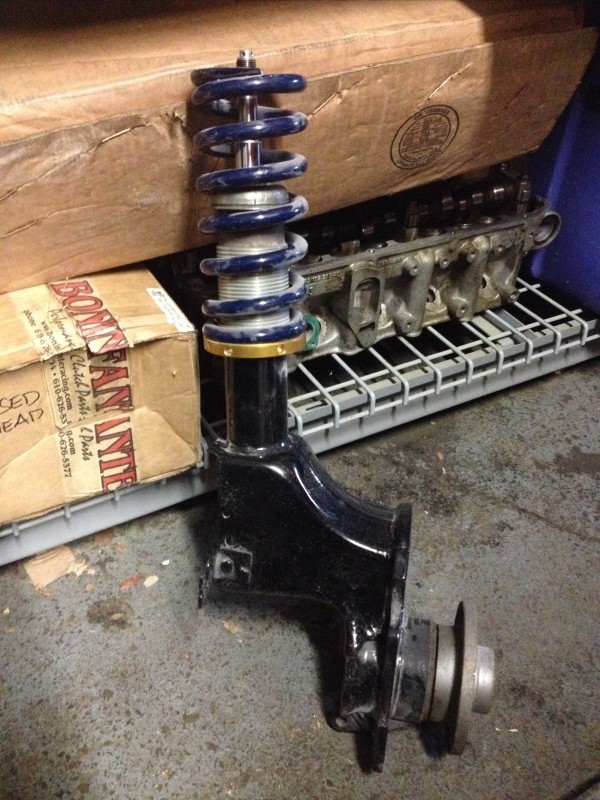
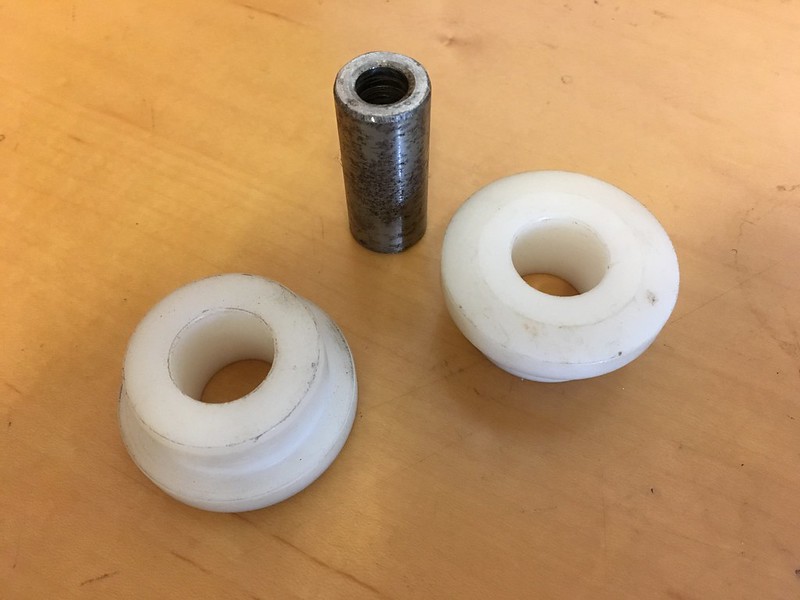
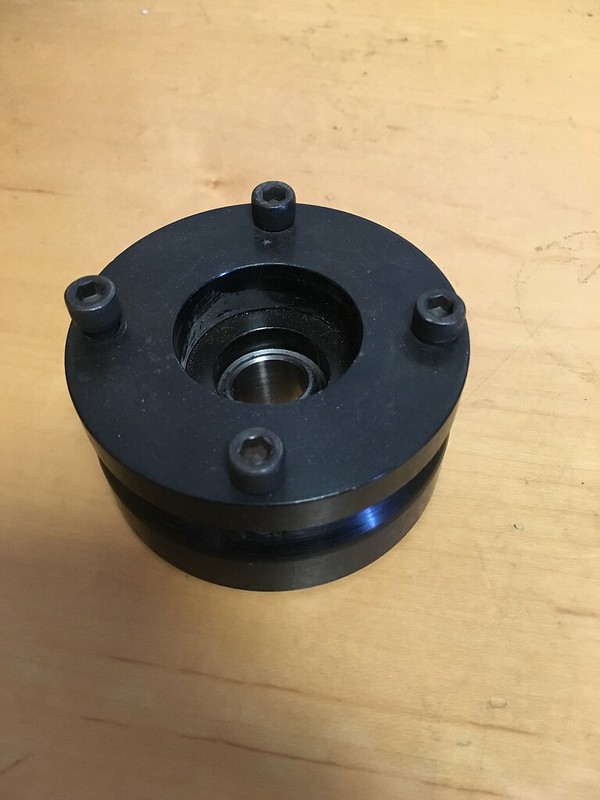
We have had an interesting time trying to get all this kit to work. Firstly the delrin bushings are wider than the sleeve that goes through them. This sleeve needs to end up slightly proud of the bushings so that it get clamped in the mounting slots and does not move. Then the bushings can rotate on the sleeve. Fortunately the sleeves appear to be the correct length.
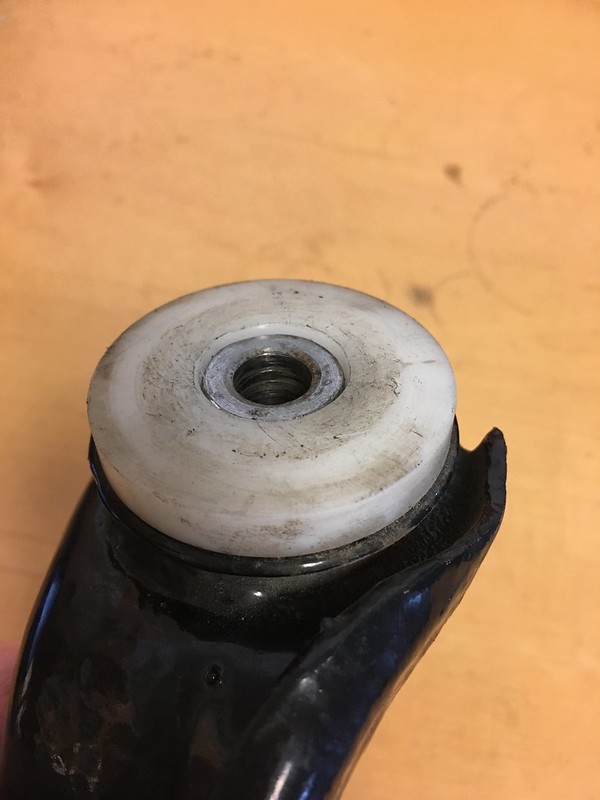
It’s a good thing the bushings are also too thick as we need to remove some material to make them shorter than the sleeves. However, the sleeves are too tight in the bushings so we will also need to relieve them a little so they will actually rotate.
The top mounts don’t work either. Early on we had some spacers made to locate the upper spring perch and get some articulation in the mount but we won’t know how much articulation we need until we can mock-up a front and rear strut and control arm, but it’s definitely going to require more than we have now.

Unfortunately, due to the amount of hardware we are introducing to allow articulation we are also using up all of the threaded portion of the strut shaft and, although we can get a nut on we can’t access the hole in the top which will allow us to stop the shaft turning so we can torque it down.

To make things more interesting we have not yet found any off the shelf tubing of the correct dimensions to use as spacers so it will all have to be made.
The tops of the struts are also unfinished. We are concerned that these may corrode, especially the threaded sleeves. We are hoping our plating shop can zinc dichromate just the top portion as paint would be too thick.
And we thought not having to stick to OE parts would make this project fun!
On a brighter note we did have some small victories with the dash. We found and mounted a VW Beetle headlight switch:
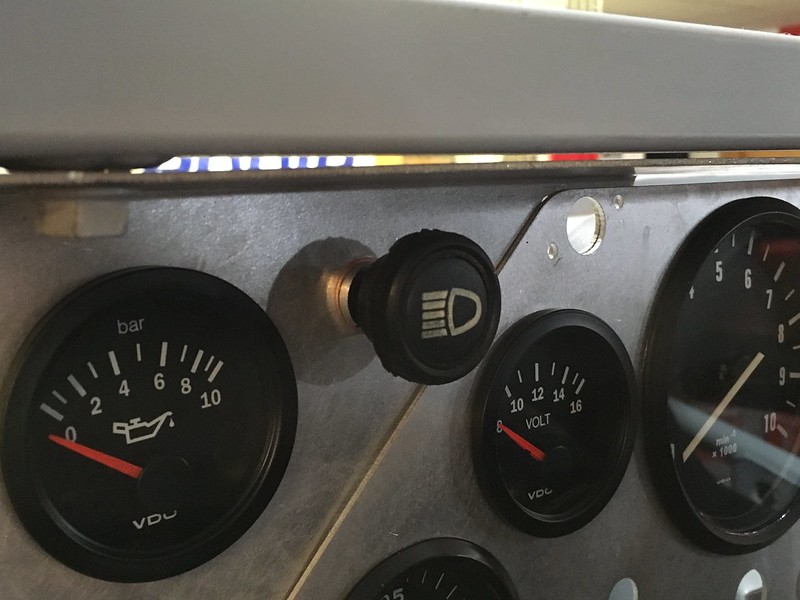
And the period correct heated rear window switch:

Next update should include how we solve all the suspension issues, hopefully.

As you may recall the car came with some suspension parts, the origin of which we could not determine. Namely: delrin control arm bushings, coil-over conversion kit and spherical bearing top mounts.

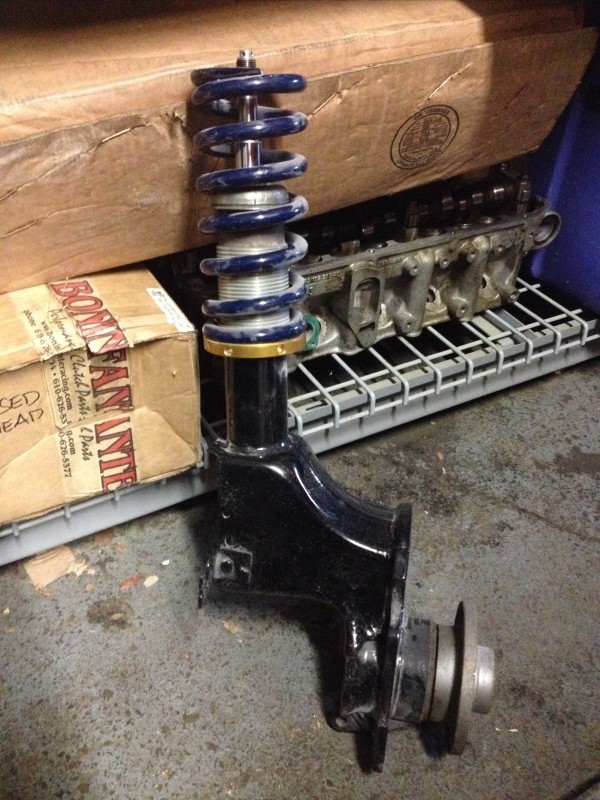
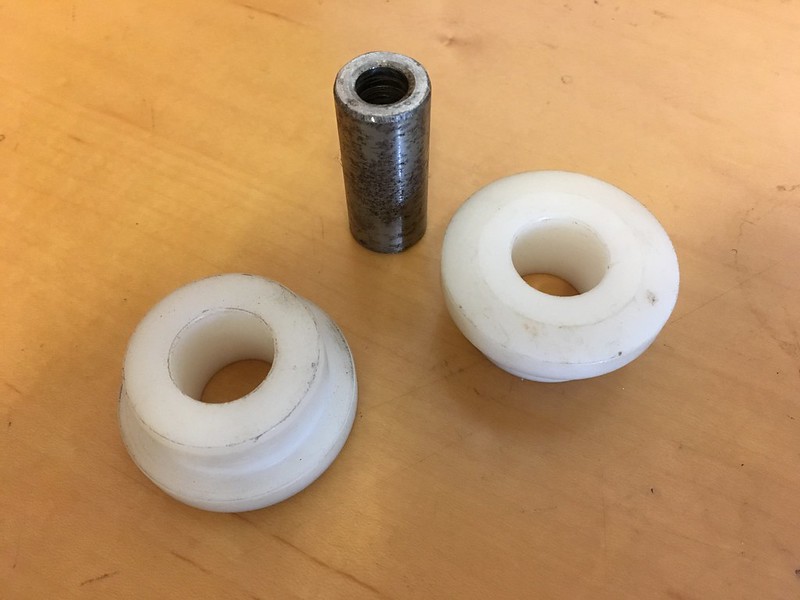
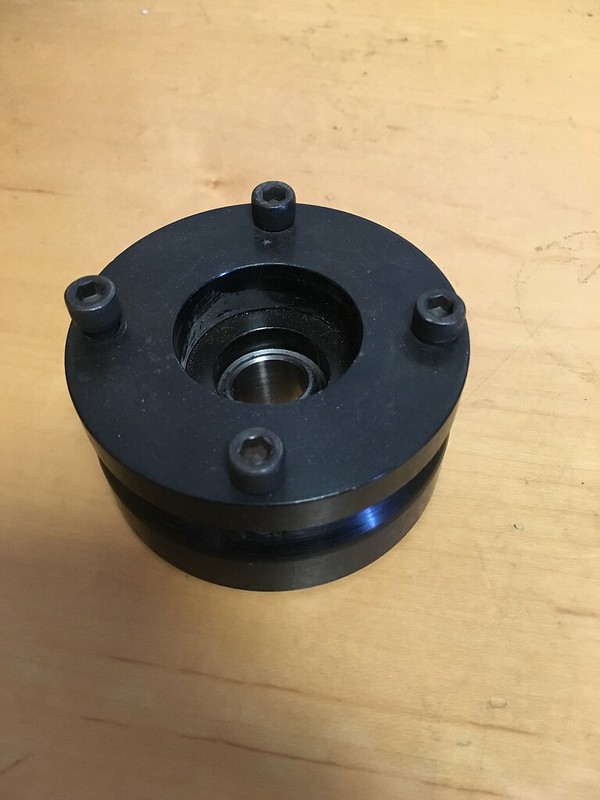
We have had an interesting time trying to get all this kit to work. Firstly the delrin bushings are wider than the sleeve that goes through them. This sleeve needs to end up slightly proud of the bushings so that it get clamped in the mounting slots and does not move. Then the bushings can rotate on the sleeve. Fortunately the sleeves appear to be the correct length.
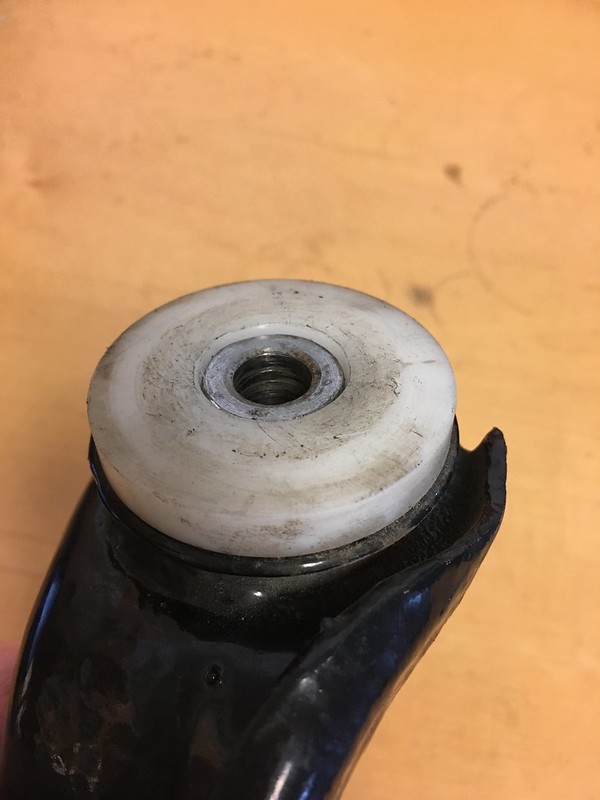
It’s a good thing the bushings are also too thick as we need to remove some material to make them shorter than the sleeves. However, the sleeves are too tight in the bushings so we will also need to relieve them a little so they will actually rotate.
The top mounts don’t work either. Early on we had some spacers made to locate the upper spring perch and get some articulation in the mount but we won’t know how much articulation we need until we can mock-up a front and rear strut and control arm, but it’s definitely going to require more than we have now.

Unfortunately, due to the amount of hardware we are introducing to allow articulation we are also using up all of the threaded portion of the strut shaft and, although we can get a nut on we can’t access the hole in the top which will allow us to stop the shaft turning so we can torque it down.

To make things more interesting we have not yet found any off the shelf tubing of the correct dimensions to use as spacers so it will all have to be made.
The tops of the struts are also unfinished. We are concerned that these may corrode, especially the threaded sleeves. We are hoping our plating shop can zinc dichromate just the top portion as paint would be too thick.
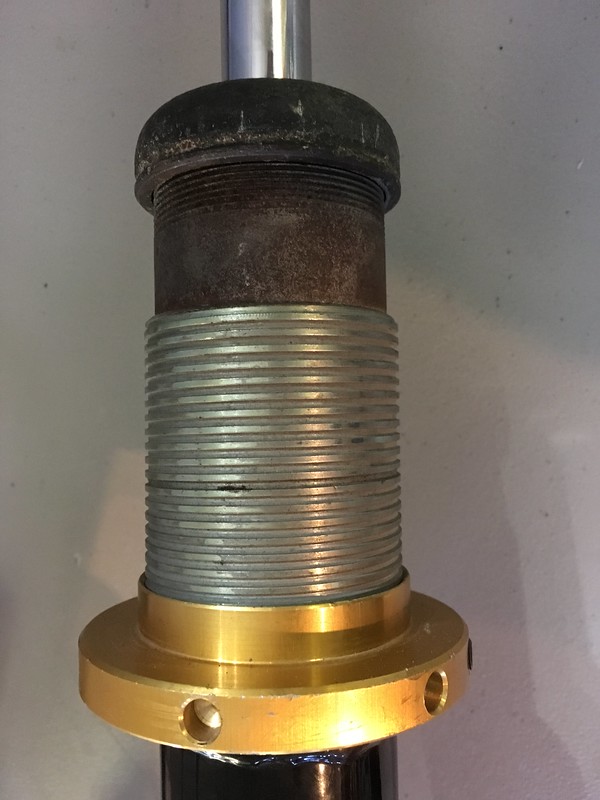
And we thought not having to stick to OE parts would make this project fun!
On a brighter note we did have some small victories with the dash. We found and mounted a VW Beetle headlight switch:
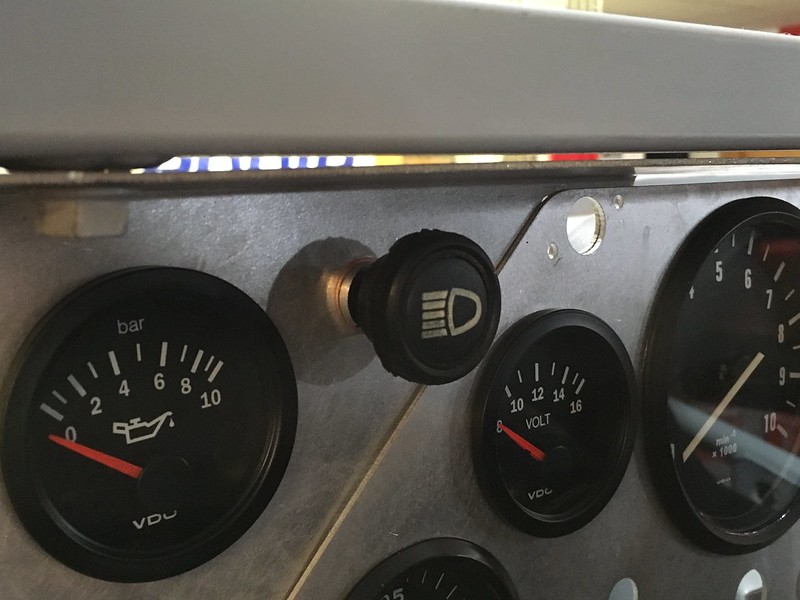
And the period correct heated rear window switch:

Next update should include how we solve all the suspension issues, hopefully.
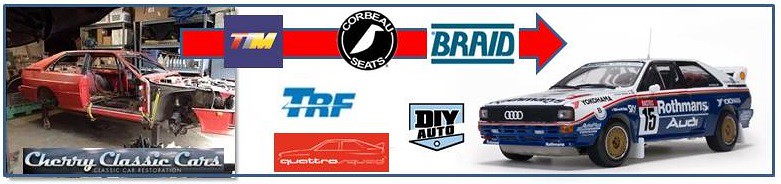
Last edited by team illuminata; 09-10-2018 at 01:08 PM.
#48

Like the suave, sophisticated gentleman in this video says “The car has legs now”
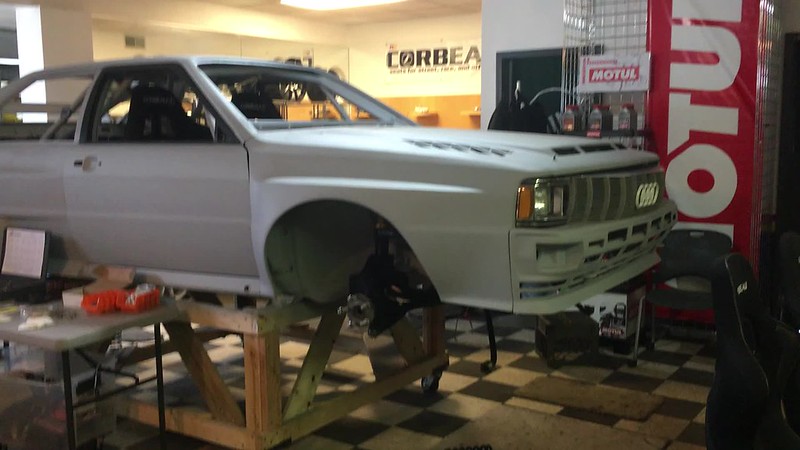
How did we get to this point? Well, as we discussed in our last post the delrin bushings are wider than the sleeve that goes through them. This sleeve needs to end up slightly proud of the bushings so that it gets clamped in the mounting slots on the subframe and does not move. Then the bushings can rotate on the sleeves. Fortunately the sleeves appear to be the correct length but they were also too tight in the bushings so we relieved them a little:
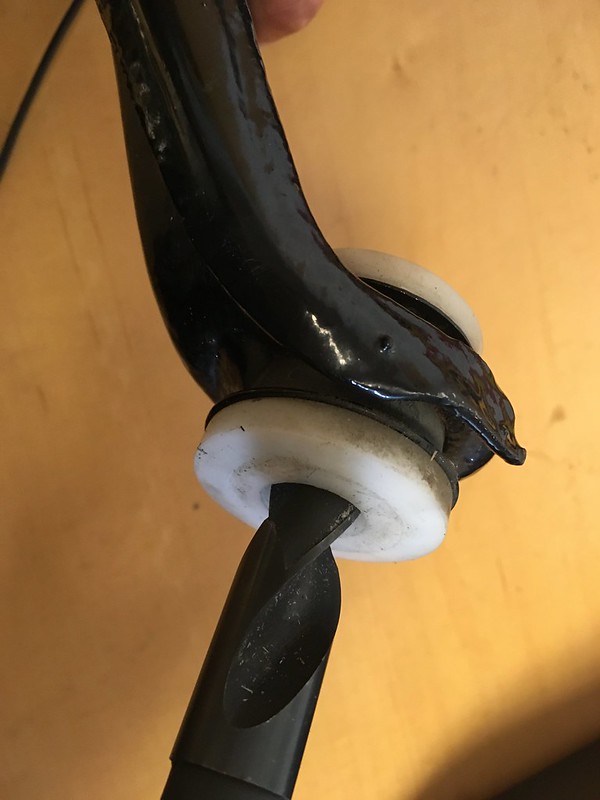
The bushings are also too thick so we removed some material to make them shorter than the sleeves and also added a chamfer so they would fit in the subframe slots:
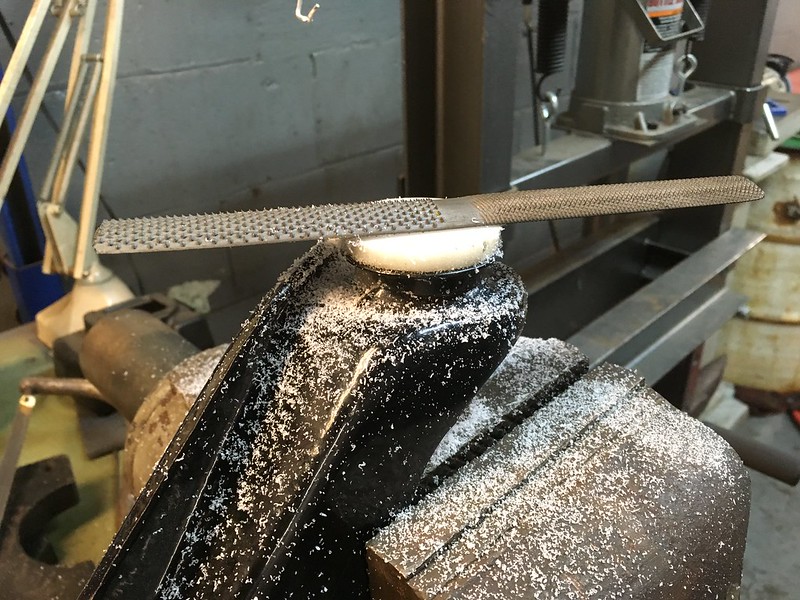

Then we had to scour the globe to find ball joints:

Our top mounts that came with the car are held in place by four set screws so we had to get the drill out again:
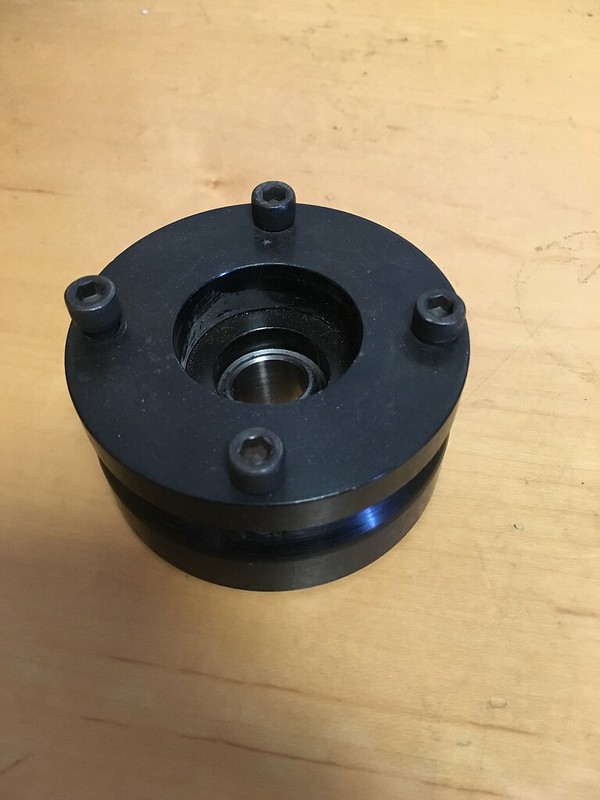
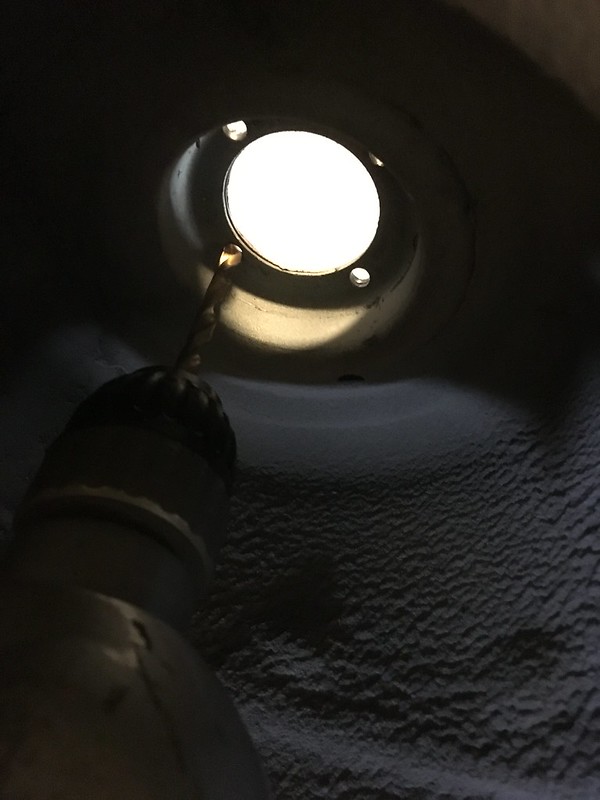
We were worried that our bearing, spacer and nut combination wouldn’t have enough articulation so we assembled a front strut and put it through its entire range to see if it would be enough. It was, thankfully:
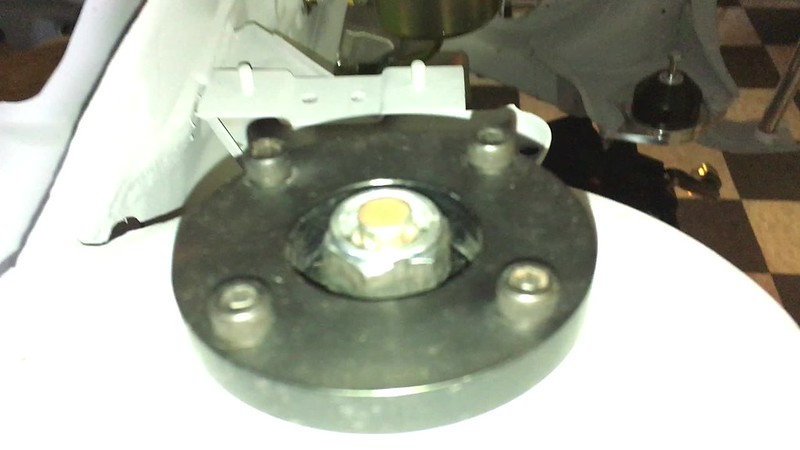
To celebrate this small milestone we threw on a wheel off our 85.

Maybe next update we’ll have figured the actual wheels and tires we will use. Maybe you can help by suggesting a wheel from the BRAID range. https://braidusa.com/collections/wheels
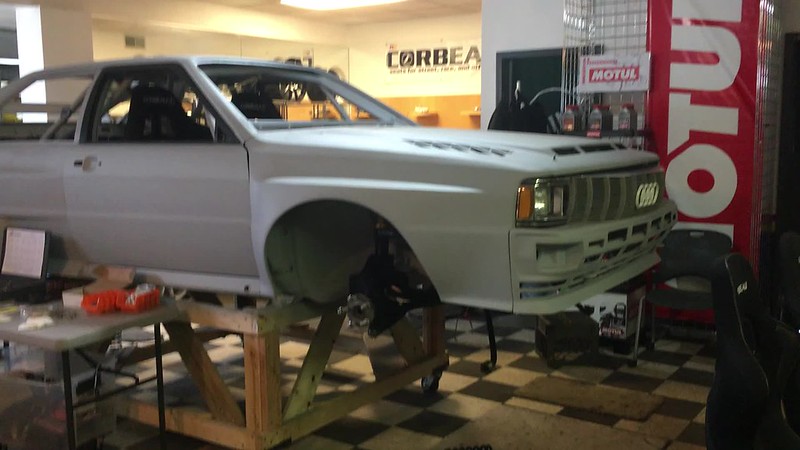
How did we get to this point? Well, as we discussed in our last post the delrin bushings are wider than the sleeve that goes through them. This sleeve needs to end up slightly proud of the bushings so that it gets clamped in the mounting slots on the subframe and does not move. Then the bushings can rotate on the sleeves. Fortunately the sleeves appear to be the correct length but they were also too tight in the bushings so we relieved them a little:
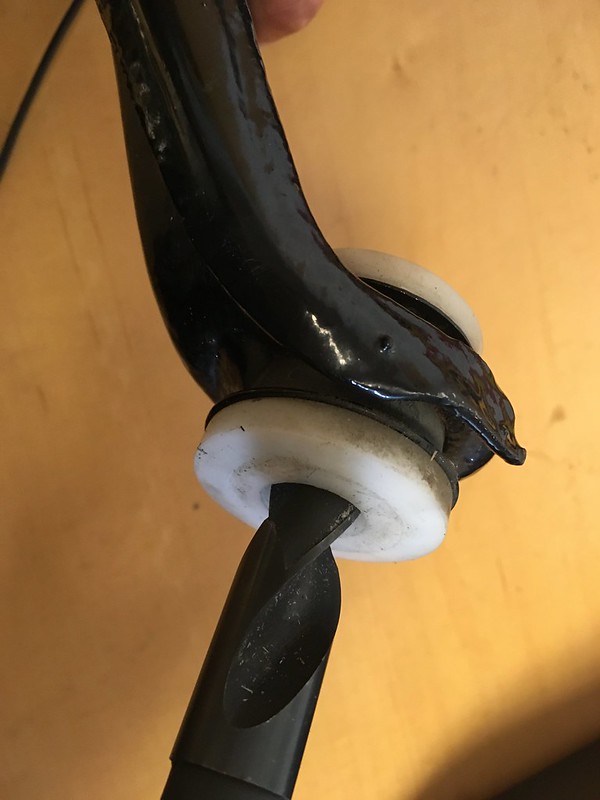
The bushings are also too thick so we removed some material to make them shorter than the sleeves and also added a chamfer so they would fit in the subframe slots:
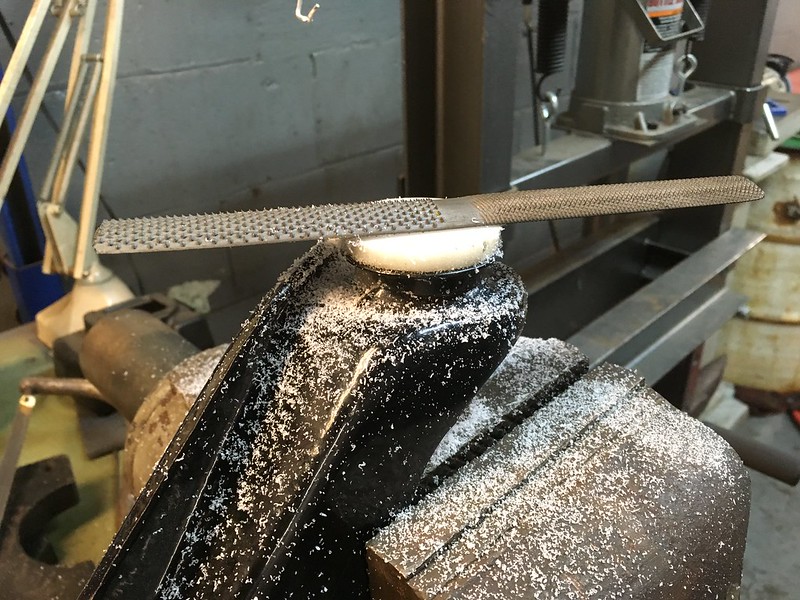

Then we had to scour the globe to find ball joints:

Our top mounts that came with the car are held in place by four set screws so we had to get the drill out again:
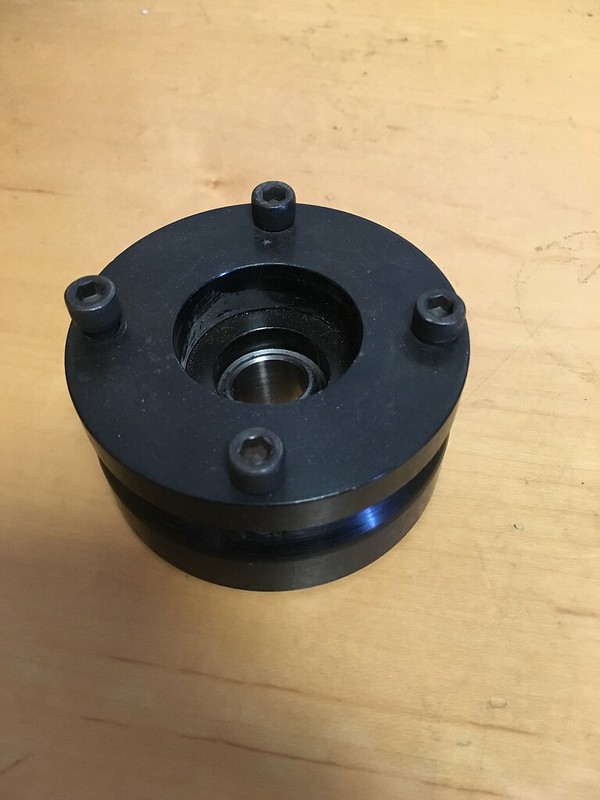
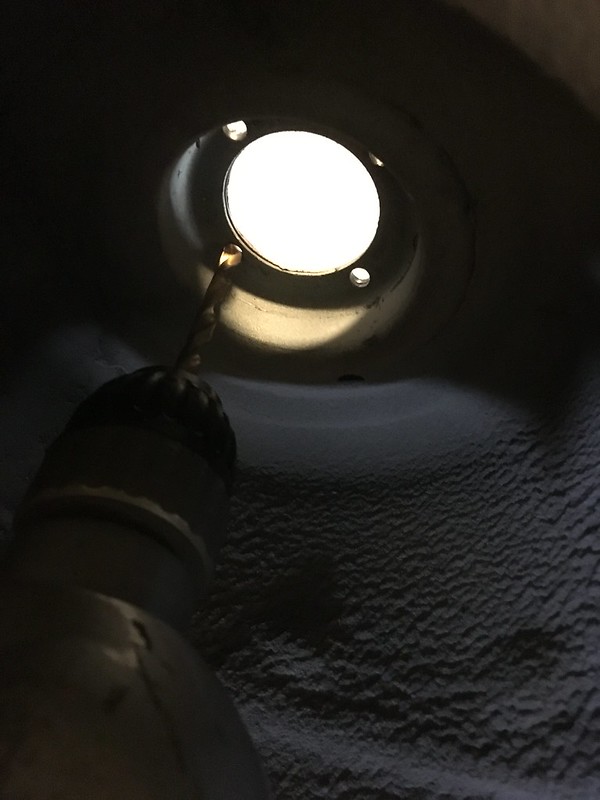
We were worried that our bearing, spacer and nut combination wouldn’t have enough articulation so we assembled a front strut and put it through its entire range to see if it would be enough. It was, thankfully:
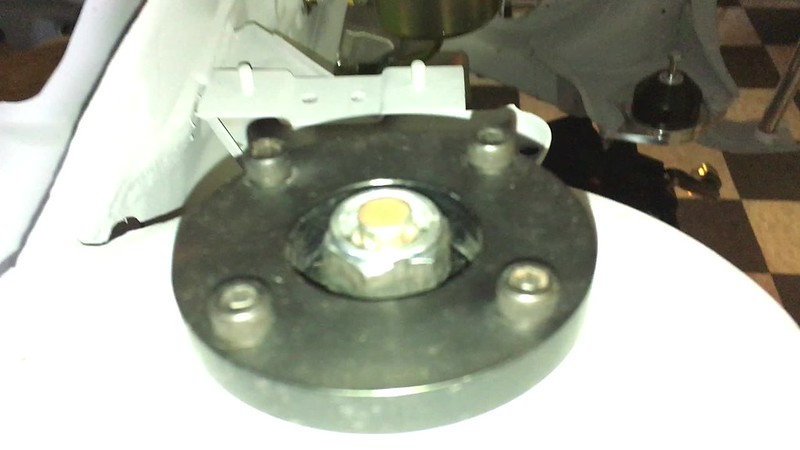
To celebrate this small milestone we threw on a wheel off our 85.

Maybe next update we’ll have figured the actual wheels and tires we will use. Maybe you can help by suggesting a wheel from the BRAID range. https://braidusa.com/collections/wheels
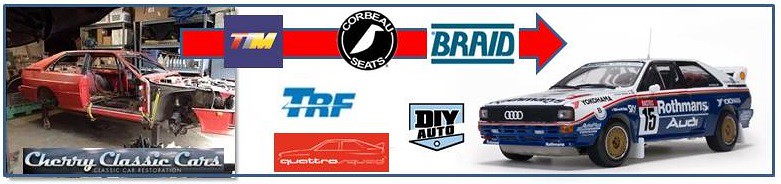
#49

TIRES
It’s time to start thinking about wheels and tires. Well, it’s a bit early but a) we are obsessed about wheels and tires and b) this project is as much about showing off our BRAID wheels as anything. At least that’s how we justify it.
You may recall we previously purchased a set of BRAID Serie 6 in 16x9 and mounted some 245/45-16 Bridgestones on them.
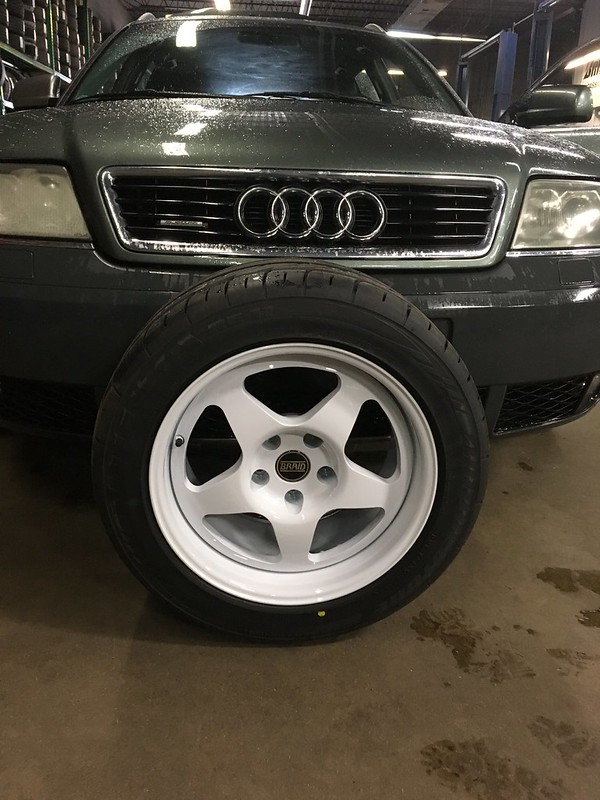
This size combination seems to be typical of what people run on these tribute cars but we ordered them way too soon (obsessed remember) and another build needed them for their project so we let them go. We always thought we would order up the exact same thing again at a more sensible phase of the project. Then we saw this:
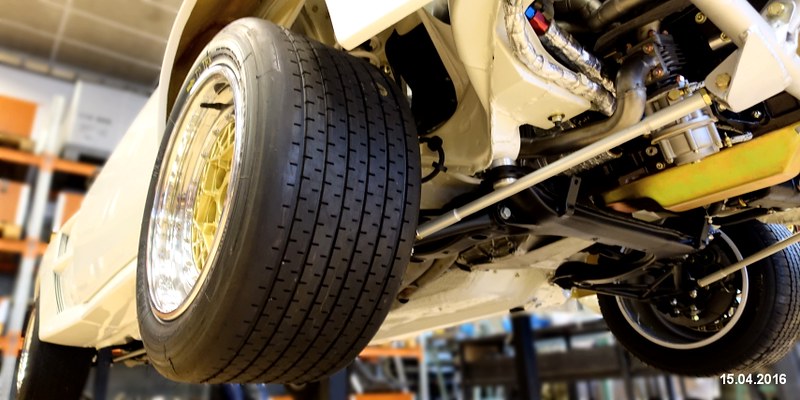

And we knew what we had to do.
We have always loved the Michelin TB15s as we sell hundreds of 911 wheels for them and they look just perfect on those RSR recreations, but we never thought we’d have a car suitable for them as the sizes they come in are either too narrow or too wide for anything we have. Or so we thought. It turns out that back in the day at least some Quattros were running the 23/59 - 15 TB15s (about a 270/40R15) so we knew they should fit on our car too. Unknown though is at what offset and rim width. Michelin only make the 23/59 – 15 in a TB5 now so we ordered up a TB15 in 23/62 – 15 from Coker tire on the condition that we could return it if we didn’t mount it. Specs for the tire are:
Section width: 10.6”/270mm
Tread width: 9”/229mm
Diameter: 24.6”/625mm
Rim width: 8.5”-10.5”
Measured rim: 9”
Unfortunately we had nothing similar in the shop to test with; or so we thought. One of our customers keeps his 944 Turbo race car in the building and it runs Hoosiers in 275/35R17. The specs on those: are
Section width: 11”/279mm
Tread width: 10.3”/261mm
Diameter: 24.7”/627mm
So just slightly larger than the TB15, apart from tread width which is quite a bit larger. We had us a surrogate.
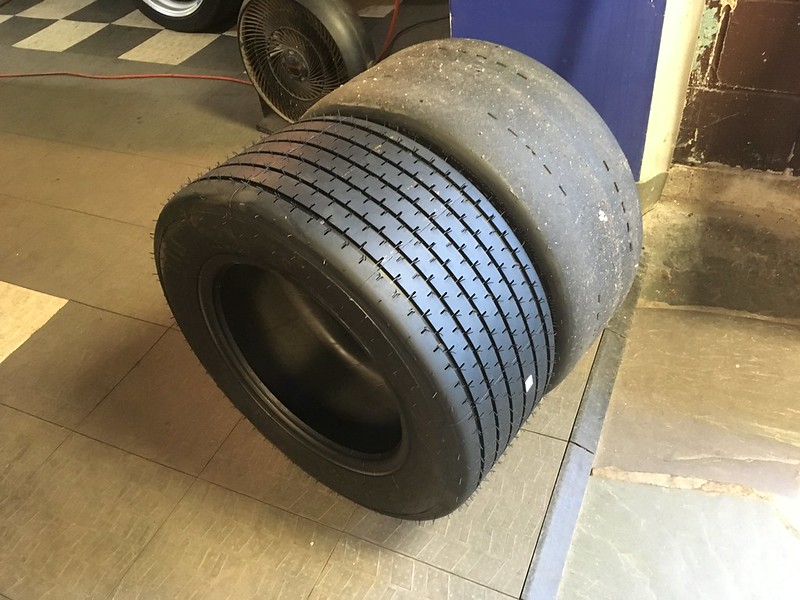
Now some of you might point out that a Porsche 944 is not going to bolt up to a Quattro. Well normally that’s right but we have some hub adapters that allow us to bolt a set of 911 Safari wheels to our Audi Allroad so we employed one of those in our test fit. The 944 wheel, which coincidentally is a BRAID Serie 6, has an offset of 55. Our hub adapter is 27 and we also have some 18mm spacers. That makes the resultant offset of the test setup et11, right about where we anticipate our new wheels need to be. Time to find out.
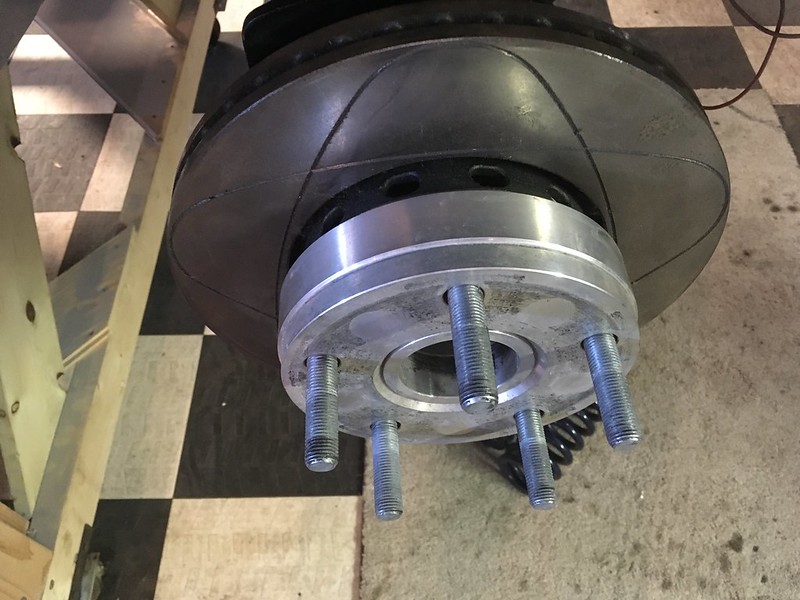
The Hoosier cleared the strut but kissed the tie rod ball joint. Not to worry, The TB15 is not as wide at that point so should clear.
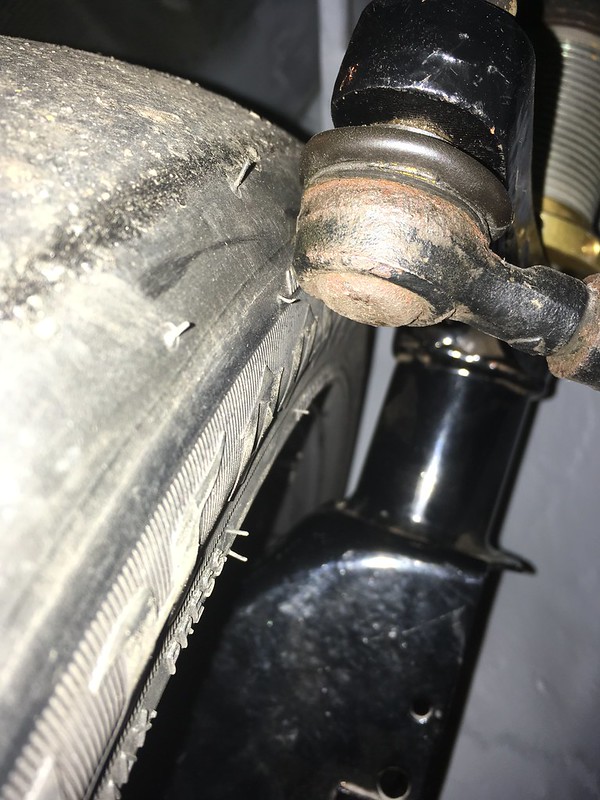
On full lock and full compression the Hoosier barley kissed the rear inner fender. OK, same as above, the TB15 should clear.

Lots of room under the front fender too:
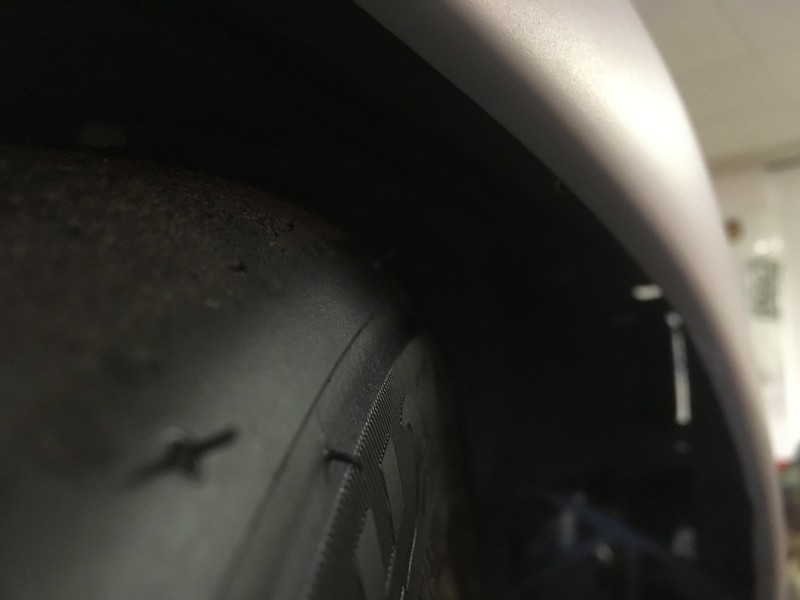

So with the front suspension in its worst orientation (full lock and full compression) the big Hoosier almost fit. We were so happy as we came away very confident that the smaller TB15 would have no issues. Still, we best throw it on the rear just for fun right? Uh oh! What’s this?
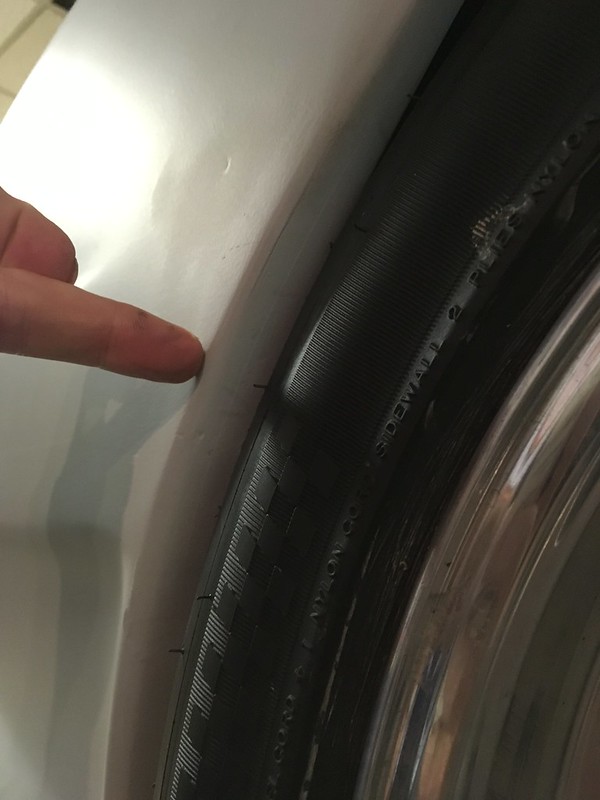
Lots of interference with the rear arch. Who would have thought? It only has to go up and down. It might fit if we tucked it in a chunk and hacked the arches up but then it might rub on the front inside and look odd. We concluded the overall diameter of the Hoosier and the TB15 precluded us from using the TB15 on this car. What to do? Well, remember the picture we found showed a much smaller diameter 23/59 -15? That size is available in a TB15 which might even be a better tread pattern for us anyway. So we returned the TB15 and ordered up Coker’s last set.
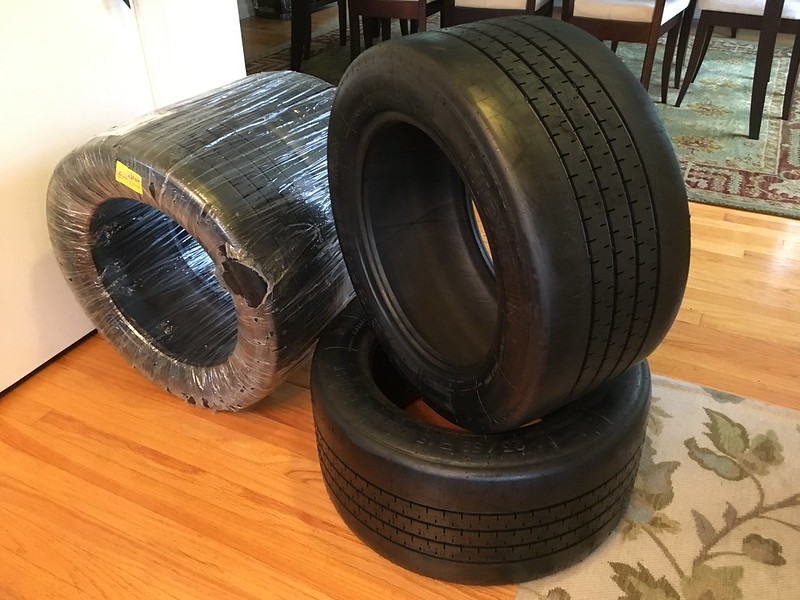
And mounted one on a 15x9 Porsche Serie 1 we had on display to see if that width would fit it well.
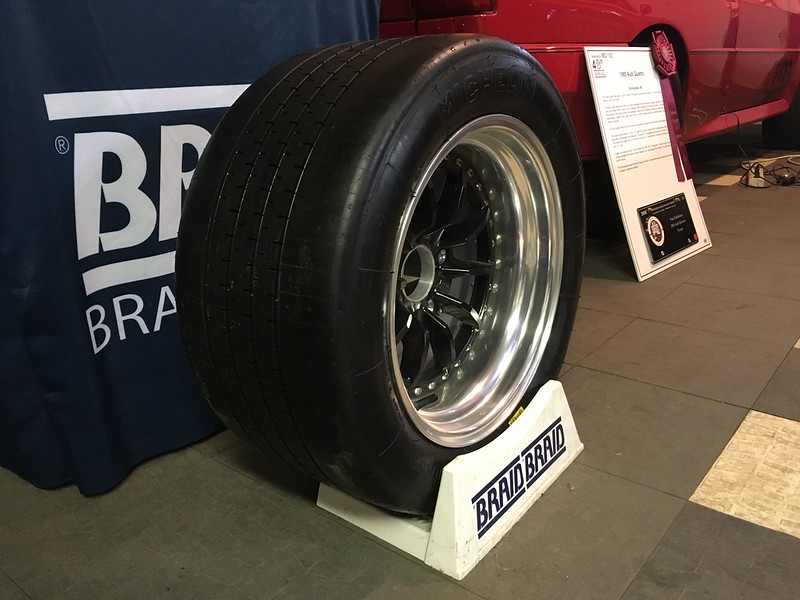
It would probably be happier on a 15x9.5 or even a 15x10 but by going with 15” we have somewhat painted ourselves into a corner, in that there aren’t any other 15” tires this wide available and who knows how long the TB5 will be around. By restricting ourselves to a 9” wide rim we have at least left the door open to some currently available and suitable 245 or even 225 tires. Hopefully we never need to go through that door.
So the next big issue to resolve: what 15x9 BRAID wheels to order to mount these on? Her are the candidates:
https://braidusa.com/collections/whe...5-x-112+15-x-9
What would you choose?
It’s time to start thinking about wheels and tires. Well, it’s a bit early but a) we are obsessed about wheels and tires and b) this project is as much about showing off our BRAID wheels as anything. At least that’s how we justify it.
You may recall we previously purchased a set of BRAID Serie 6 in 16x9 and mounted some 245/45-16 Bridgestones on them.
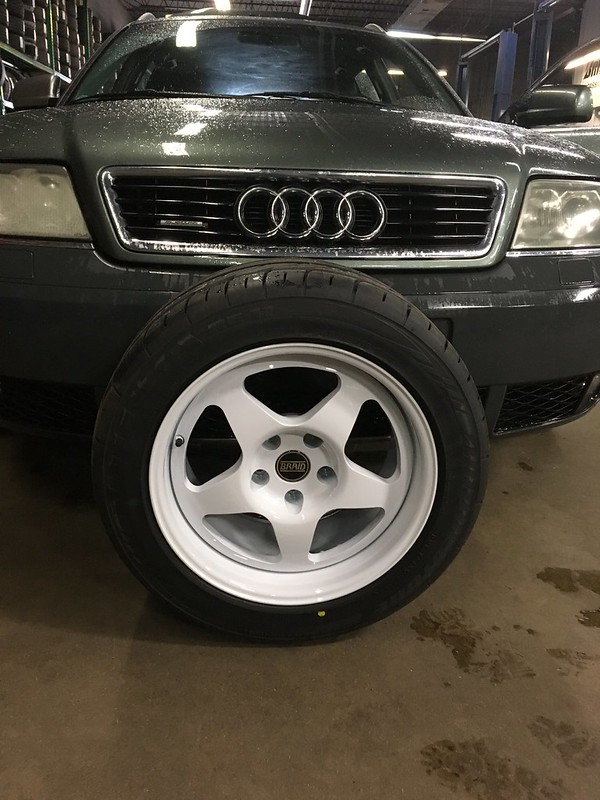
This size combination seems to be typical of what people run on these tribute cars but we ordered them way too soon (obsessed remember) and another build needed them for their project so we let them go. We always thought we would order up the exact same thing again at a more sensible phase of the project. Then we saw this:
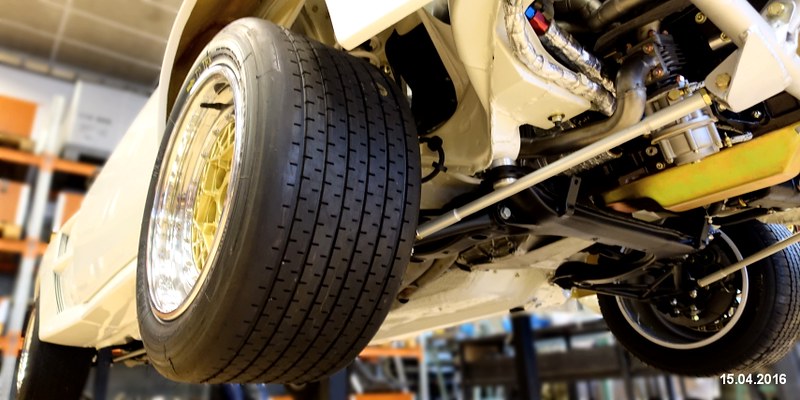

And we knew what we had to do.
We have always loved the Michelin TB15s as we sell hundreds of 911 wheels for them and they look just perfect on those RSR recreations, but we never thought we’d have a car suitable for them as the sizes they come in are either too narrow or too wide for anything we have. Or so we thought. It turns out that back in the day at least some Quattros were running the 23/59 - 15 TB15s (about a 270/40R15) so we knew they should fit on our car too. Unknown though is at what offset and rim width. Michelin only make the 23/59 – 15 in a TB5 now so we ordered up a TB15 in 23/62 – 15 from Coker tire on the condition that we could return it if we didn’t mount it. Specs for the tire are:
Section width: 10.6”/270mm
Tread width: 9”/229mm
Diameter: 24.6”/625mm
Rim width: 8.5”-10.5”
Measured rim: 9”
Unfortunately we had nothing similar in the shop to test with; or so we thought. One of our customers keeps his 944 Turbo race car in the building and it runs Hoosiers in 275/35R17. The specs on those: are
Section width: 11”/279mm
Tread width: 10.3”/261mm
Diameter: 24.7”/627mm
So just slightly larger than the TB15, apart from tread width which is quite a bit larger. We had us a surrogate.
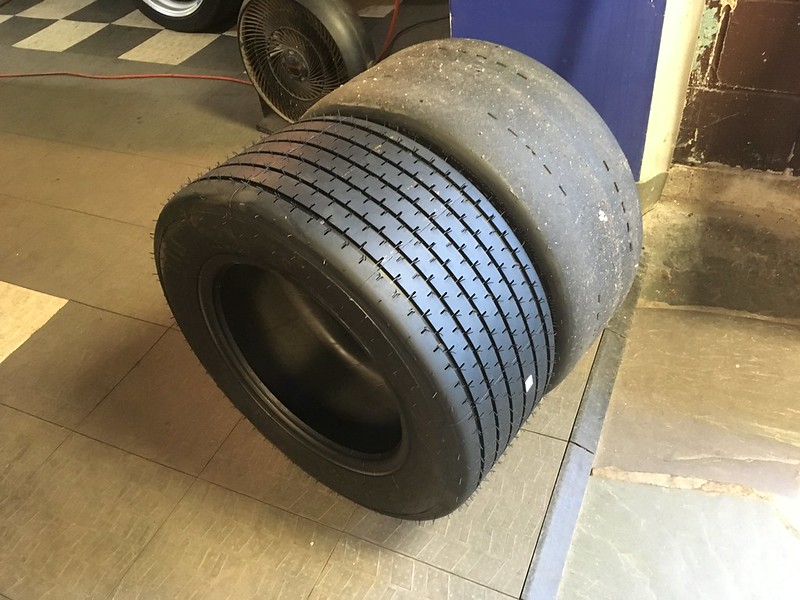
Now some of you might point out that a Porsche 944 is not going to bolt up to a Quattro. Well normally that’s right but we have some hub adapters that allow us to bolt a set of 911 Safari wheels to our Audi Allroad so we employed one of those in our test fit. The 944 wheel, which coincidentally is a BRAID Serie 6, has an offset of 55. Our hub adapter is 27 and we also have some 18mm spacers. That makes the resultant offset of the test setup et11, right about where we anticipate our new wheels need to be. Time to find out.
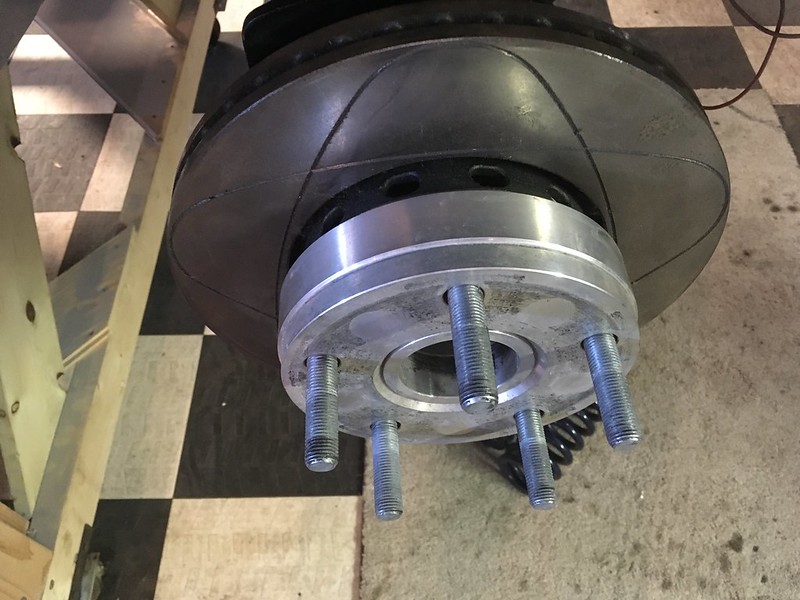
The Hoosier cleared the strut but kissed the tie rod ball joint. Not to worry, The TB15 is not as wide at that point so should clear.
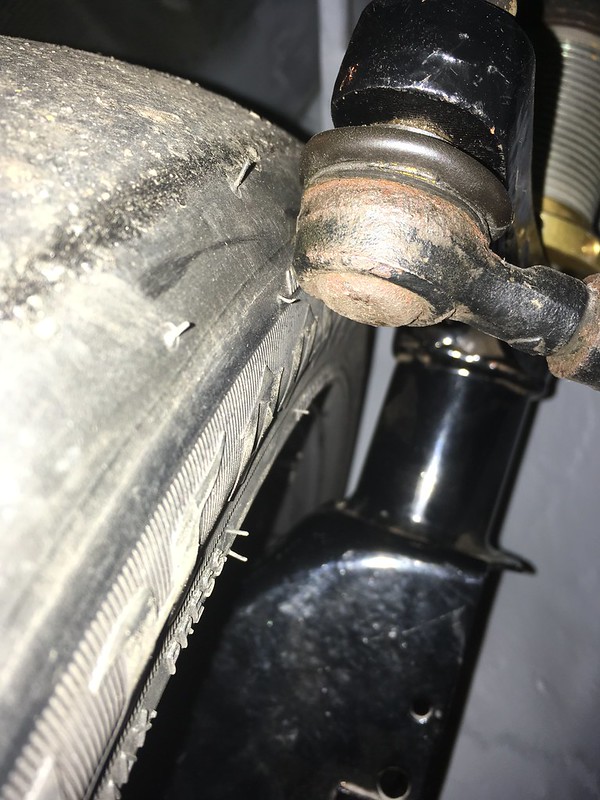
On full lock and full compression the Hoosier barley kissed the rear inner fender. OK, same as above, the TB15 should clear.

Lots of room under the front fender too:
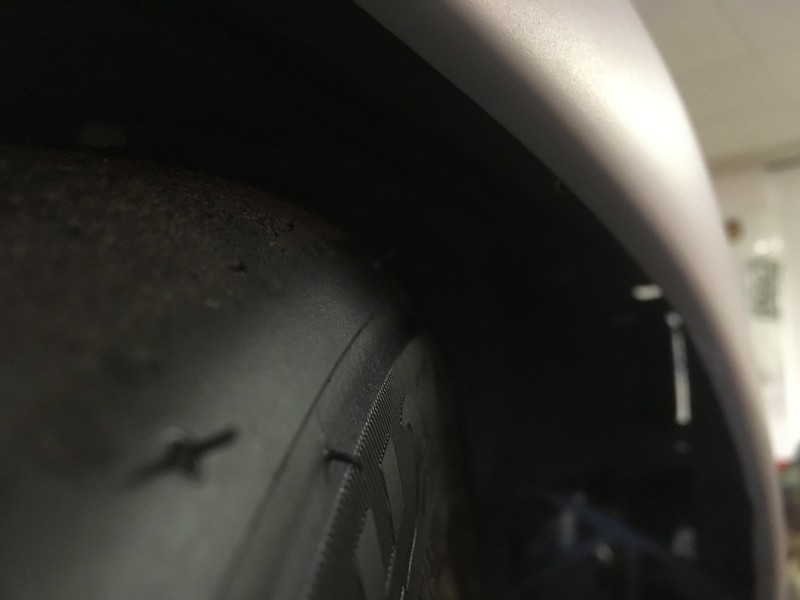

So with the front suspension in its worst orientation (full lock and full compression) the big Hoosier almost fit. We were so happy as we came away very confident that the smaller TB15 would have no issues. Still, we best throw it on the rear just for fun right? Uh oh! What’s this?
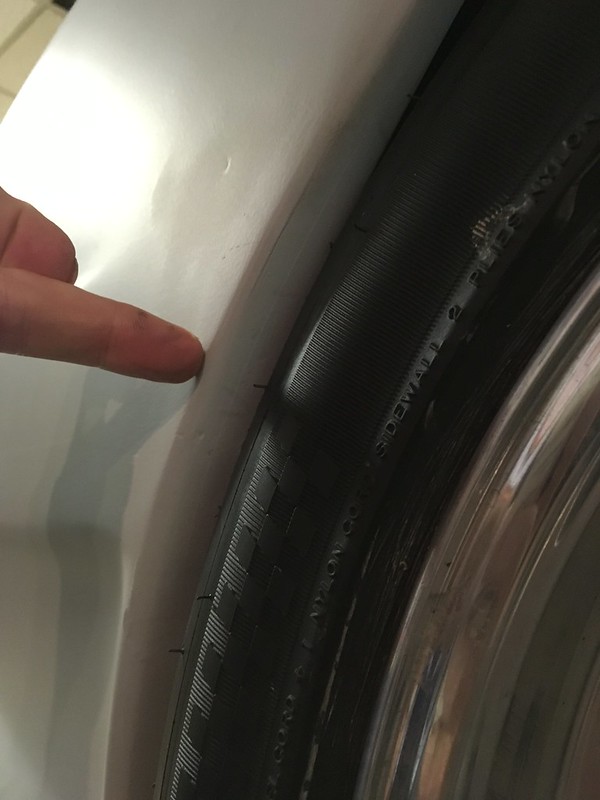
Lots of interference with the rear arch. Who would have thought? It only has to go up and down. It might fit if we tucked it in a chunk and hacked the arches up but then it might rub on the front inside and look odd. We concluded the overall diameter of the Hoosier and the TB15 precluded us from using the TB15 on this car. What to do? Well, remember the picture we found showed a much smaller diameter 23/59 -15? That size is available in a TB15 which might even be a better tread pattern for us anyway. So we returned the TB15 and ordered up Coker’s last set.
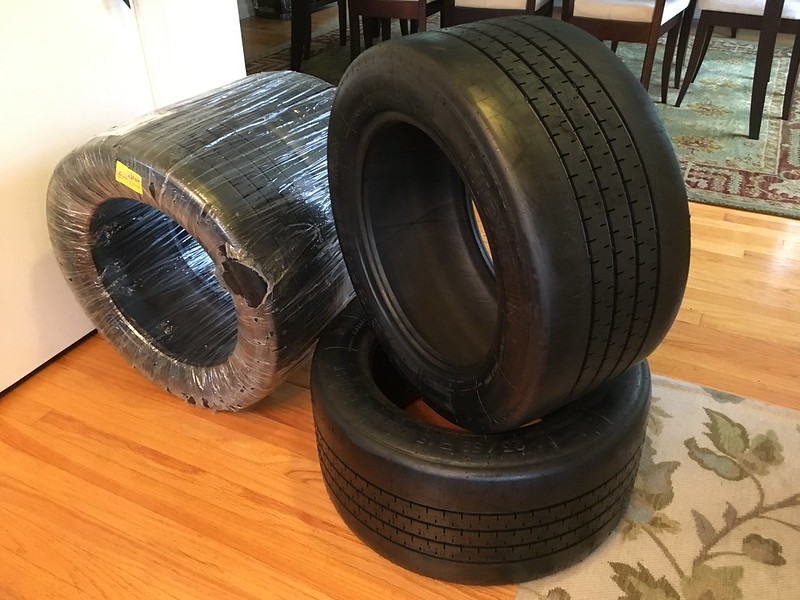
And mounted one on a 15x9 Porsche Serie 1 we had on display to see if that width would fit it well.
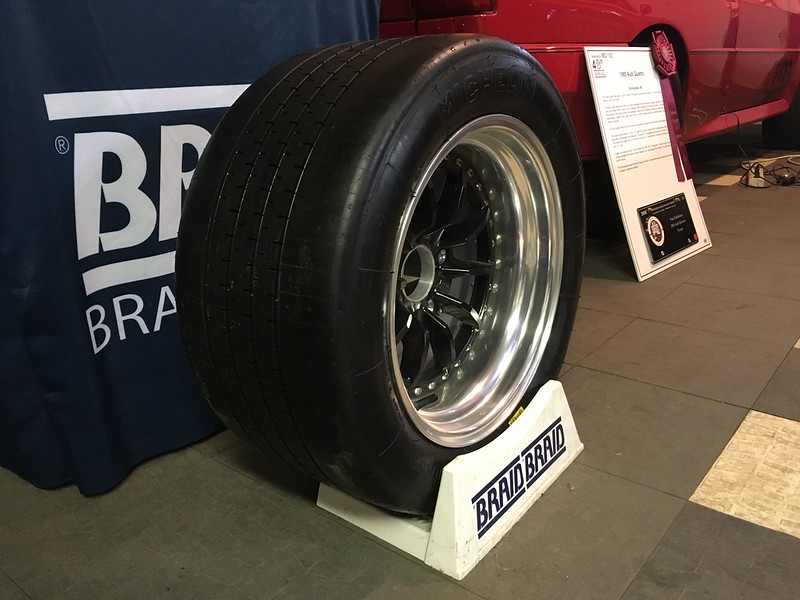
It would probably be happier on a 15x9.5 or even a 15x10 but by going with 15” we have somewhat painted ourselves into a corner, in that there aren’t any other 15” tires this wide available and who knows how long the TB5 will be around. By restricting ourselves to a 9” wide rim we have at least left the door open to some currently available and suitable 245 or even 225 tires. Hopefully we never need to go through that door.
So the next big issue to resolve: what 15x9 BRAID wheels to order to mount these on? Her are the candidates:
https://braidusa.com/collections/whe...5-x-112+15-x-9
What would you choose?
#50

Installation was relatively simple as we kept all the hardware.

Then we remembered that we also have a broken reflector which we thought would be better used on this car rather than the pristine one that came off it as we are going to be wrapping it anyway a la Rothmans livery:

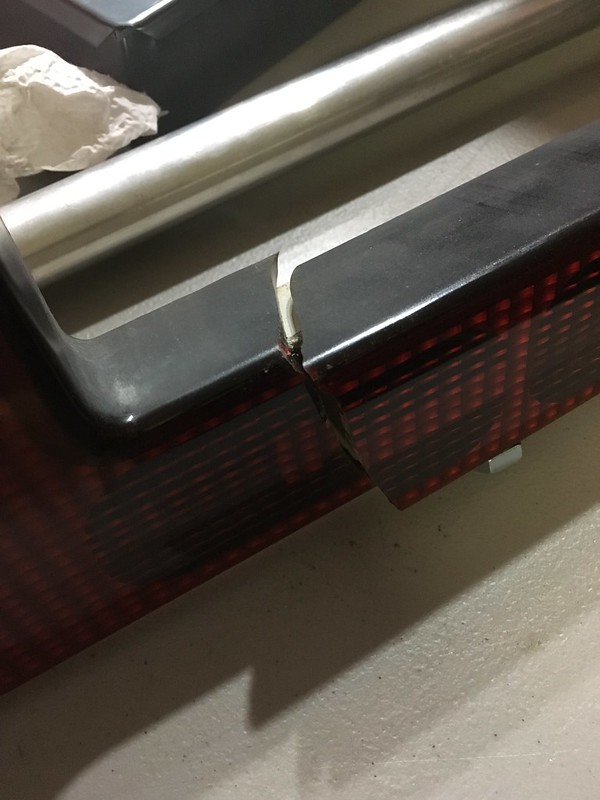
But how to fix the crack? It can be unsightly but has to be smooth as any hint of a crack will show up through the vinyl film. Fortunately one of our guys has a lot of experience with plastic adhesive and managed a nearly invisible repair.
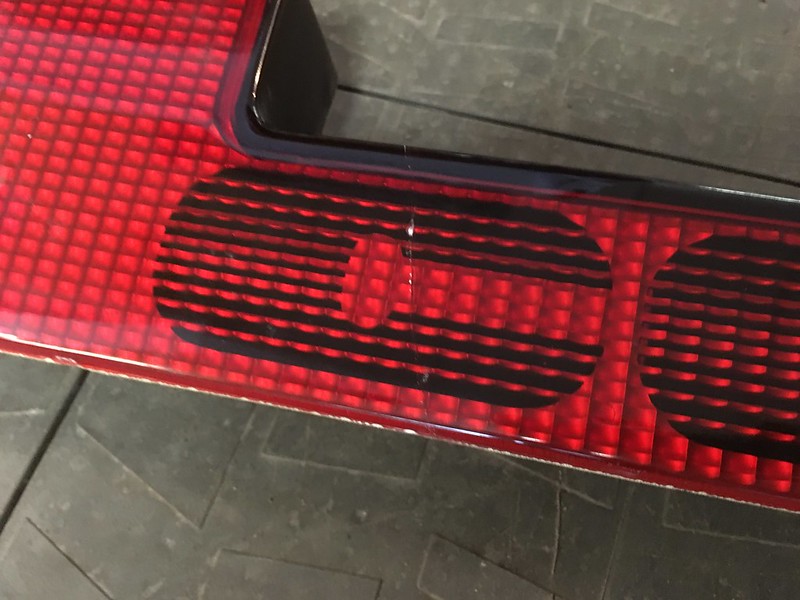

Now we have to figure out how to wrap the black side pieces. As they have horizontal grooves running along their lengths they won't take vinyl very well. We could try to paint them but it might not match the vinyl and we'd be ruining a set. We have considered filling the grooves with body filler and sanding them flat. That would wrap easily but we'd still be ruining a set. Currently considering making new filler panels. Fortunately we don't have to decide for a while though.
(BULKHEAD)
More rear of the car projects. Another piece (two actually) that would be better stored in the car is the rear bulkhead. It comes in two parts: a lower and an upper. The upper part is essentially a parcel shelf as it is mostly horizontal but is definitely not flat. No parcels will be stored here. We think this will be just a test fit as it may be in and out a lot in the course of the build, though it will be going to paint with it fully installed. It will definitely need to come out to allow us to clean up the aperture edges. Looks like that was cut with a torch.
Both pieces clearly needed to go through the side window openings. The lower panel fell into place without much trouble.
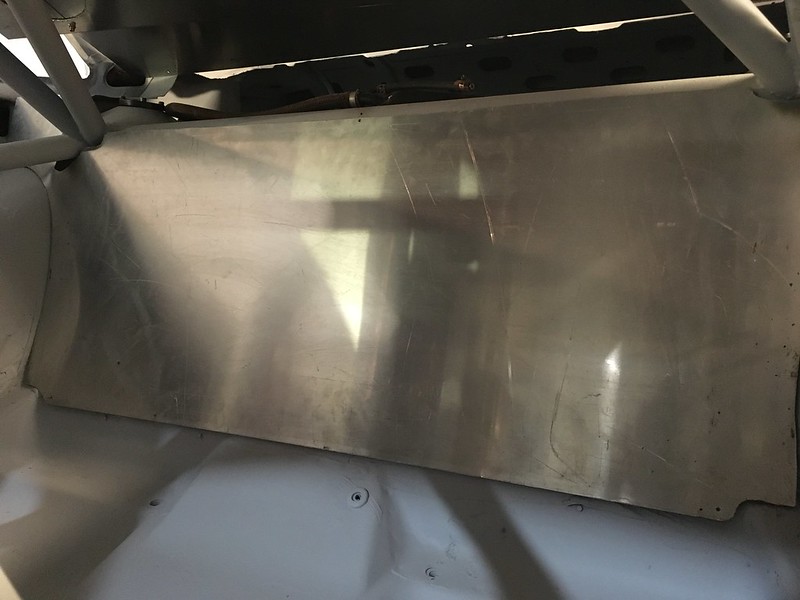
But the upper one fought us hard. We even called the cage builder and the body shop; the last people to mess with it but they couldn't remember how they did it. At least we now had the confidence to know that it does fit so we continued to jiggle it around and look for a way in. This seemed like the way it wanted to go but it wouldn't slide any further back.
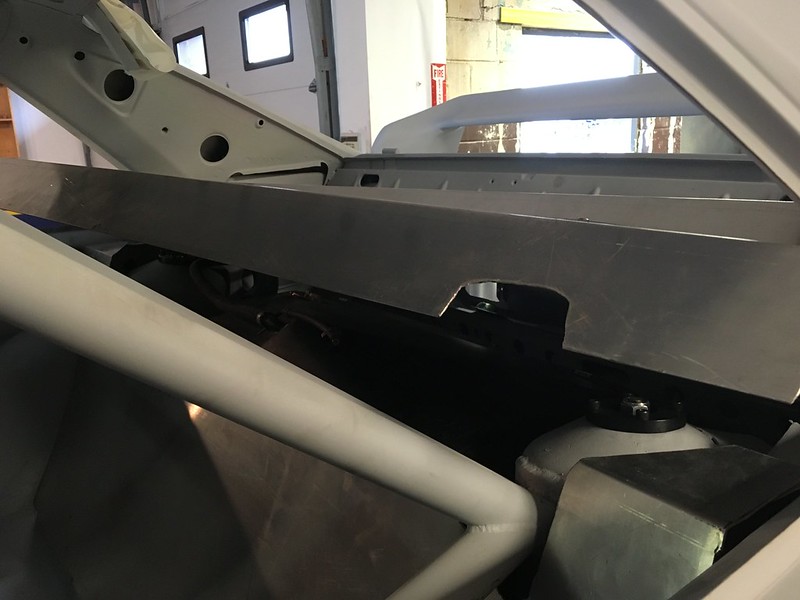
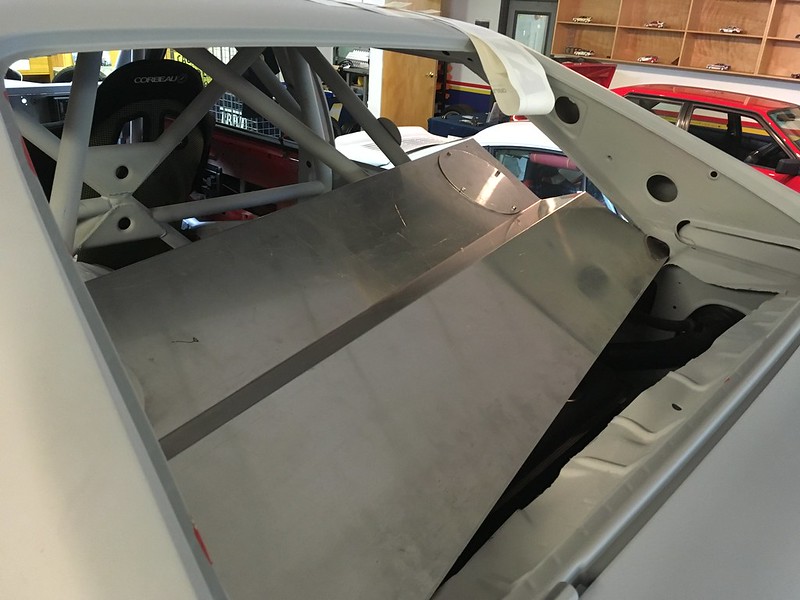
Eventually we sort of curved it as we slid it down the cage bars and then it fit nice and snug.
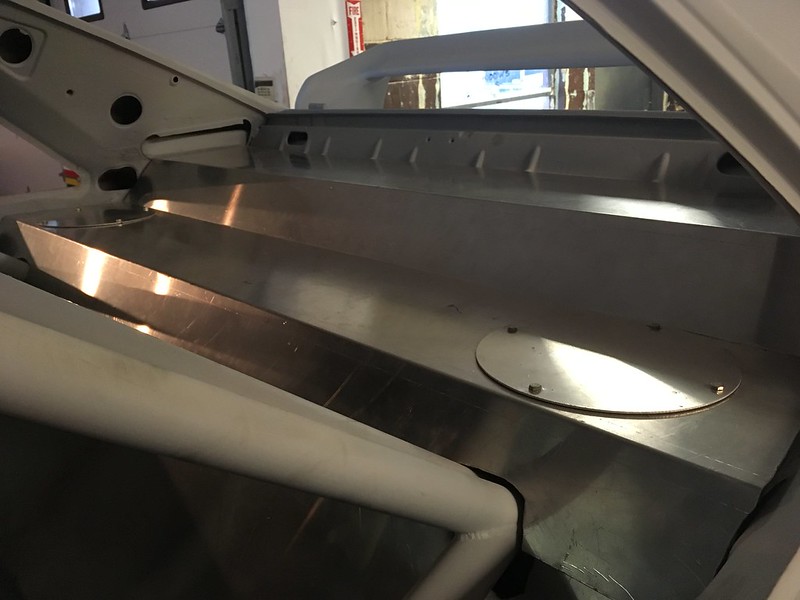

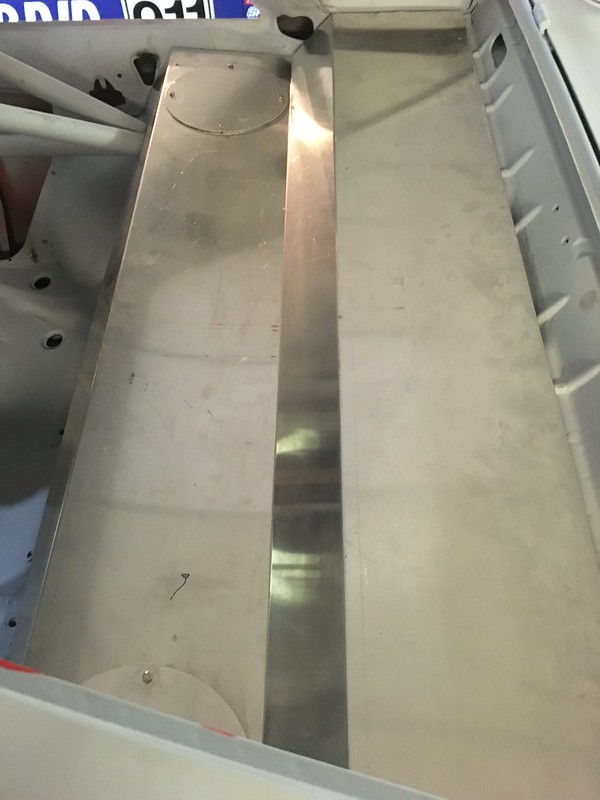
Now we have to get it out again!
(DASH)
Work continues on the dash, bit by bit. We bought an old rally computer that came off a Rothmans car in the middle east. It has no internal parts but we have another one that does and that may find its way into the car eventually. For now this one is easier to install.
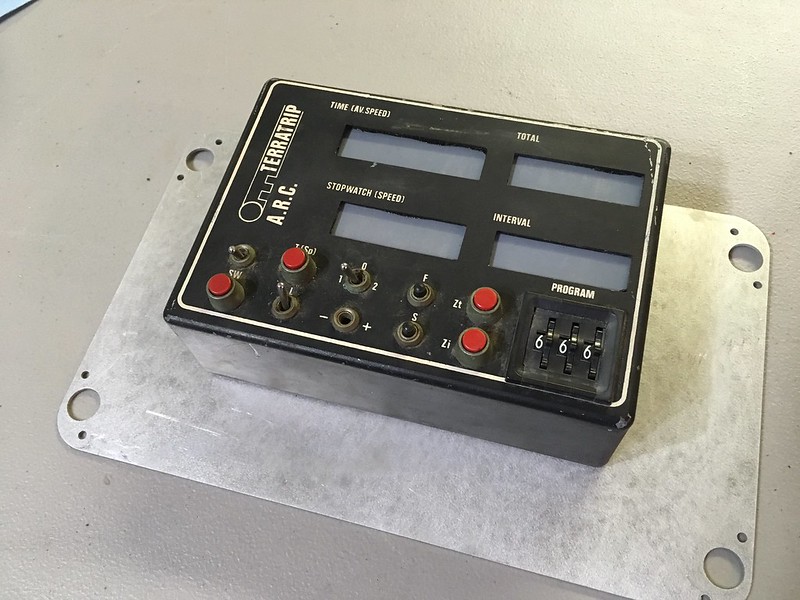
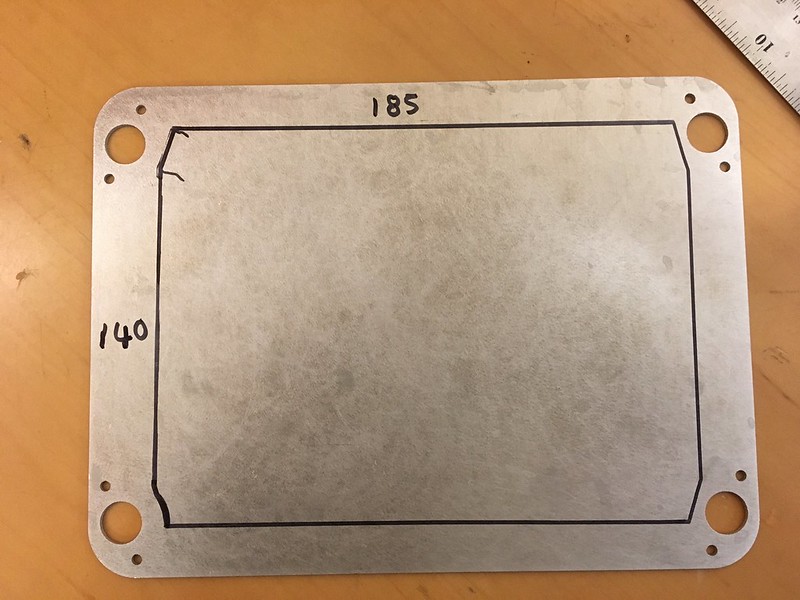
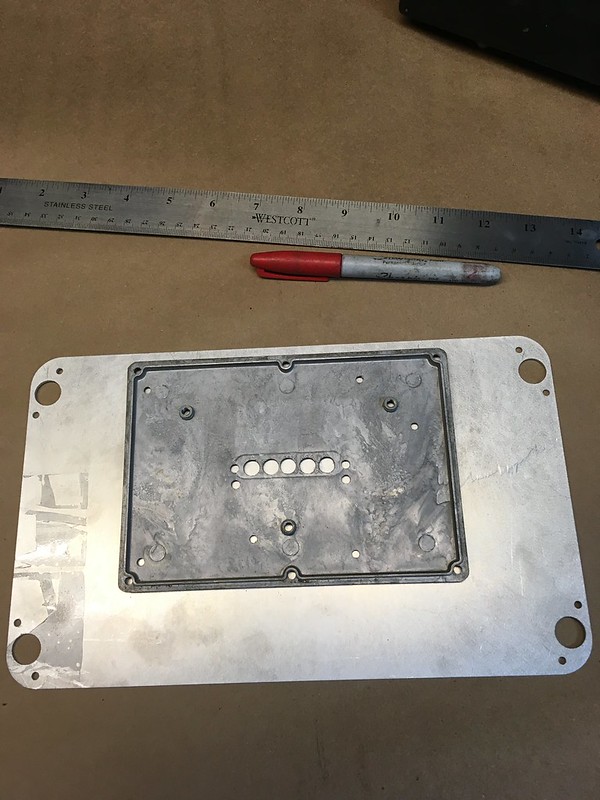
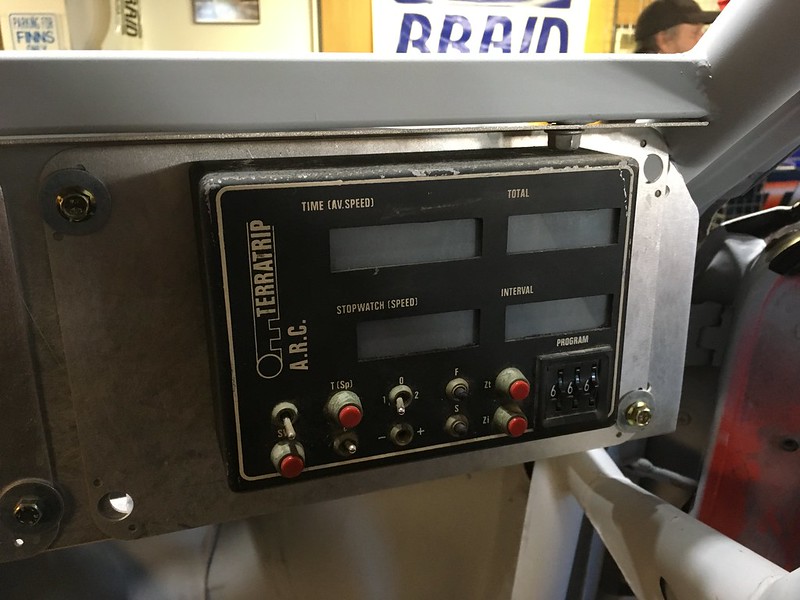
Then we thought we'd have some fun.

We just need to repaint one of the 911s and get a Rothmans Quattro model (on order) and we'll have a perfect set!
FUEL TANK
While we seem to be working on the rear of the car we thought we'd throw in the fuel tank. It's big and takes up a lot of space on the parts shelf. What more rationalization do you need. Oh, we also want to see where the fuels lines exit the trunk area so we can figure out where to locate lines, pumps and filters etc.
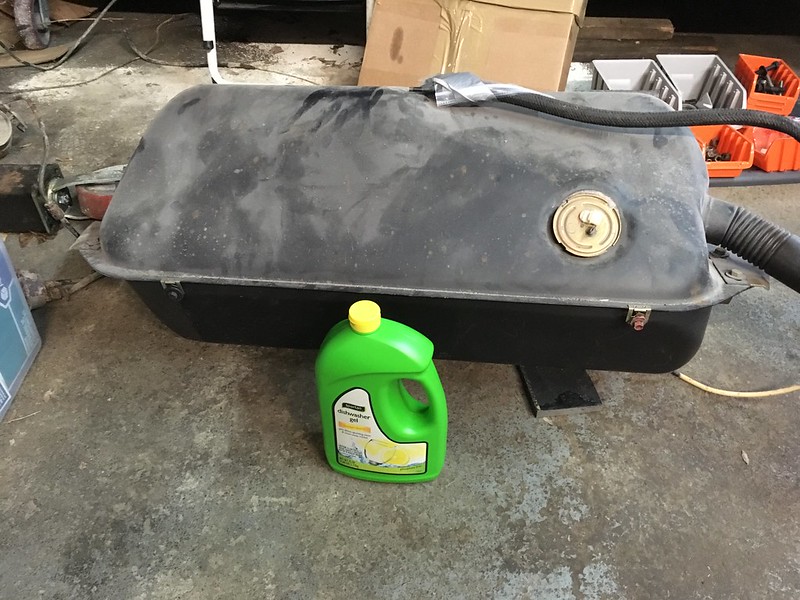
It was a bit awkward to wrestle into location, but soon cooperated.

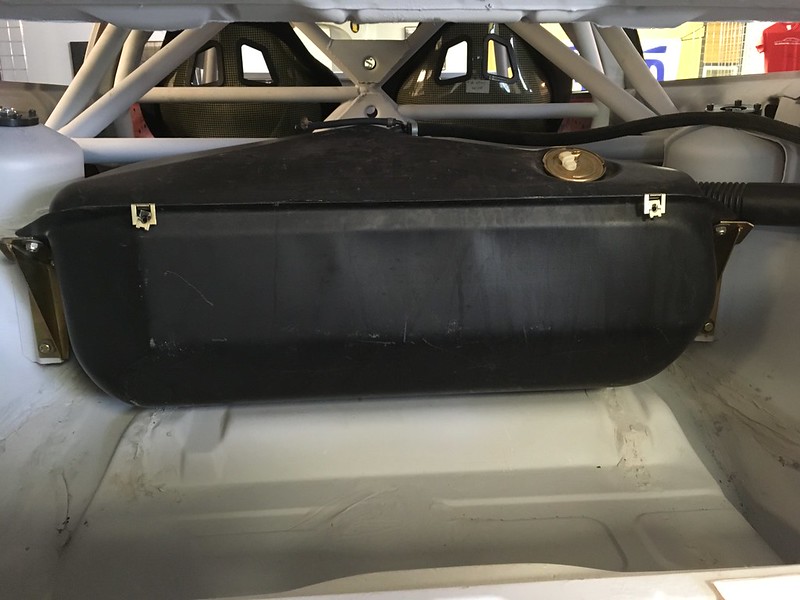

The fuel lines protrude through the trunk floor. Perhaps we can extended them through the lower rear bulkhead and mount the fuel pump/s in the cabin.

Then we remembered that we also have a broken reflector which we thought would be better used on this car rather than the pristine one that came off it as we are going to be wrapping it anyway a la Rothmans livery:

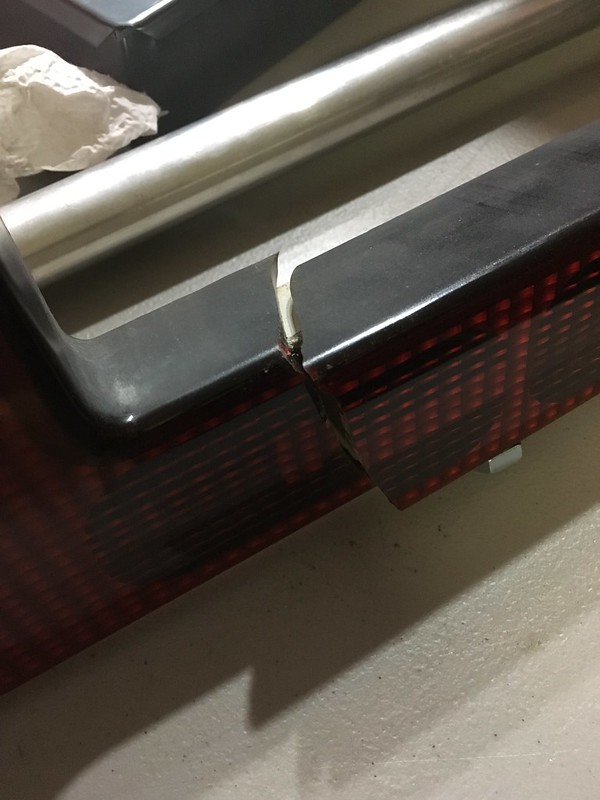
But how to fix the crack? It can be unsightly but has to be smooth as any hint of a crack will show up through the vinyl film. Fortunately one of our guys has a lot of experience with plastic adhesive and managed a nearly invisible repair.
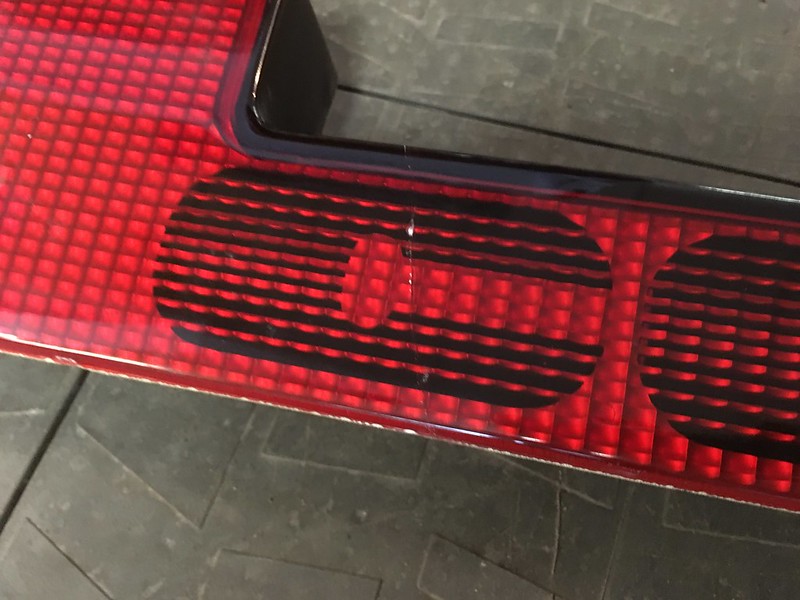

Now we have to figure out how to wrap the black side pieces. As they have horizontal grooves running along their lengths they won't take vinyl very well. We could try to paint them but it might not match the vinyl and we'd be ruining a set. We have considered filling the grooves with body filler and sanding them flat. That would wrap easily but we'd still be ruining a set. Currently considering making new filler panels. Fortunately we don't have to decide for a while though.
(BULKHEAD)
More rear of the car projects. Another piece (two actually) that would be better stored in the car is the rear bulkhead. It comes in two parts: a lower and an upper. The upper part is essentially a parcel shelf as it is mostly horizontal but is definitely not flat. No parcels will be stored here. We think this will be just a test fit as it may be in and out a lot in the course of the build, though it will be going to paint with it fully installed. It will definitely need to come out to allow us to clean up the aperture edges. Looks like that was cut with a torch.
Both pieces clearly needed to go through the side window openings. The lower panel fell into place without much trouble.
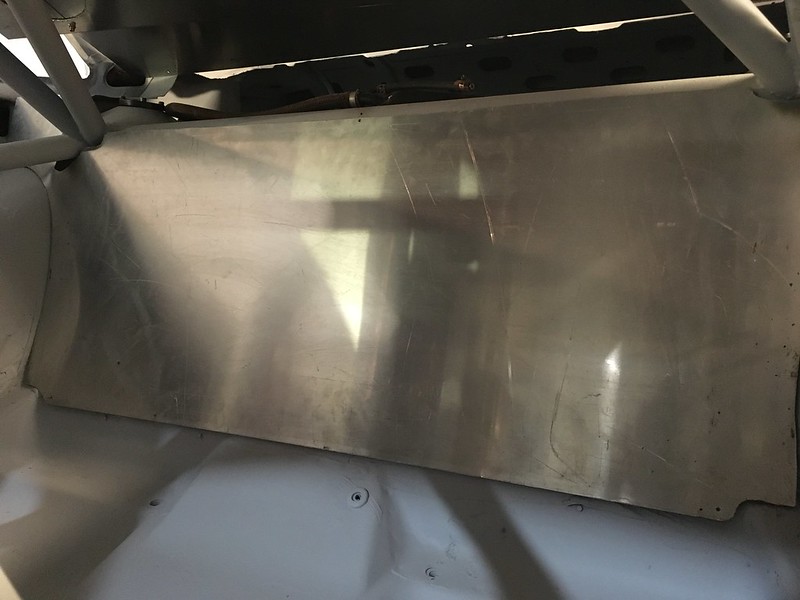
But the upper one fought us hard. We even called the cage builder and the body shop; the last people to mess with it but they couldn't remember how they did it. At least we now had the confidence to know that it does fit so we continued to jiggle it around and look for a way in. This seemed like the way it wanted to go but it wouldn't slide any further back.
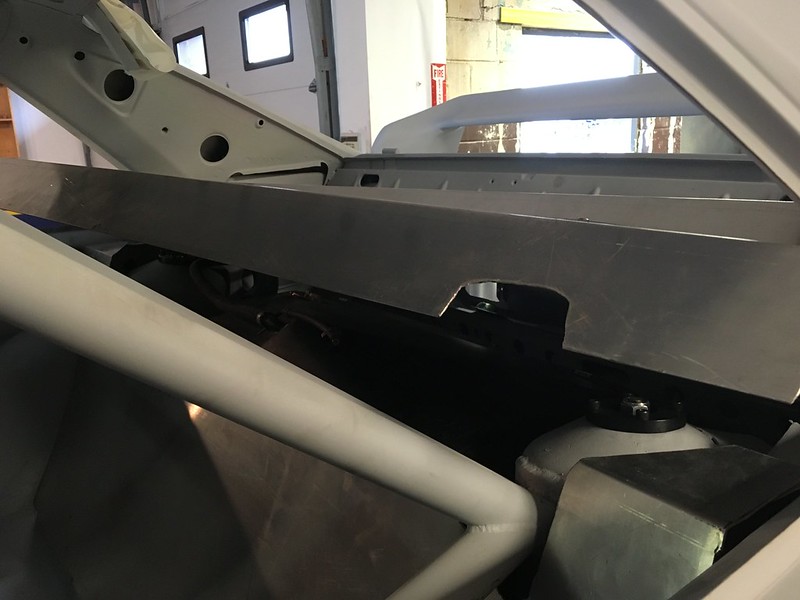
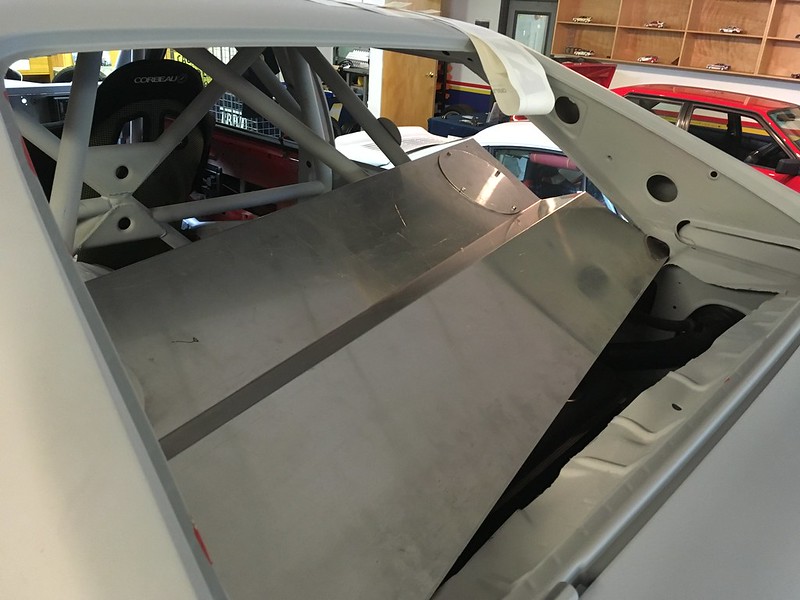
Eventually we sort of curved it as we slid it down the cage bars and then it fit nice and snug.
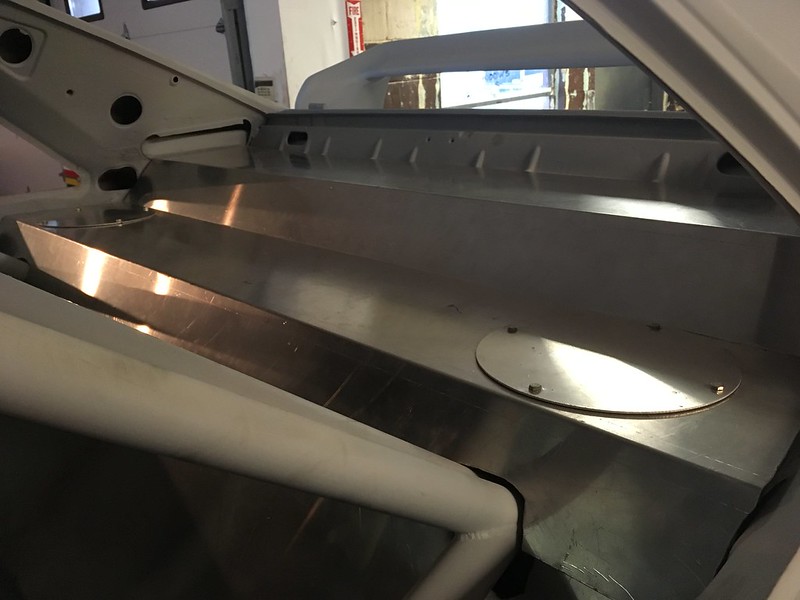

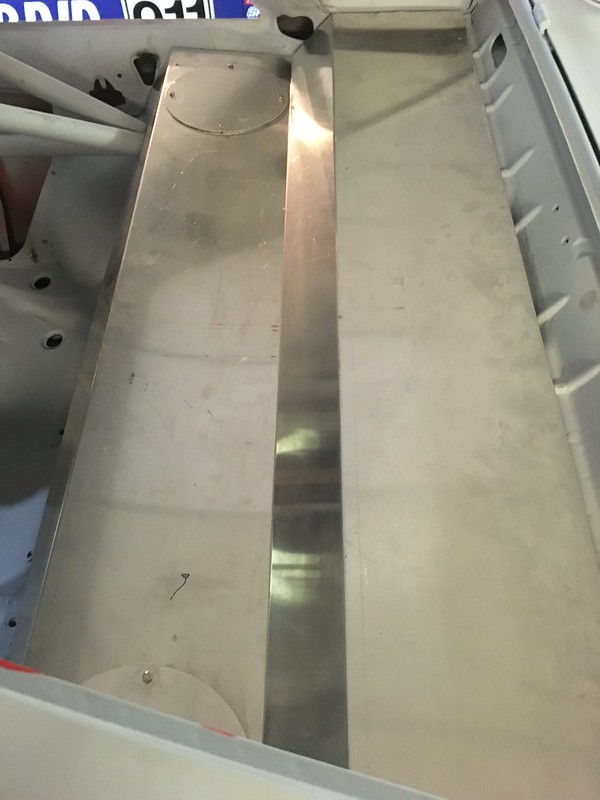
Now we have to get it out again!
(DASH)
Work continues on the dash, bit by bit. We bought an old rally computer that came off a Rothmans car in the middle east. It has no internal parts but we have another one that does and that may find its way into the car eventually. For now this one is easier to install.
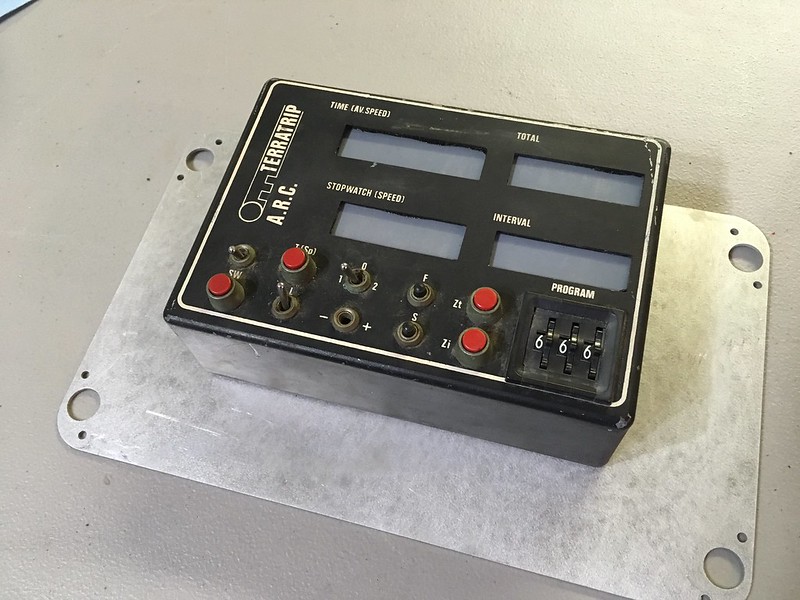
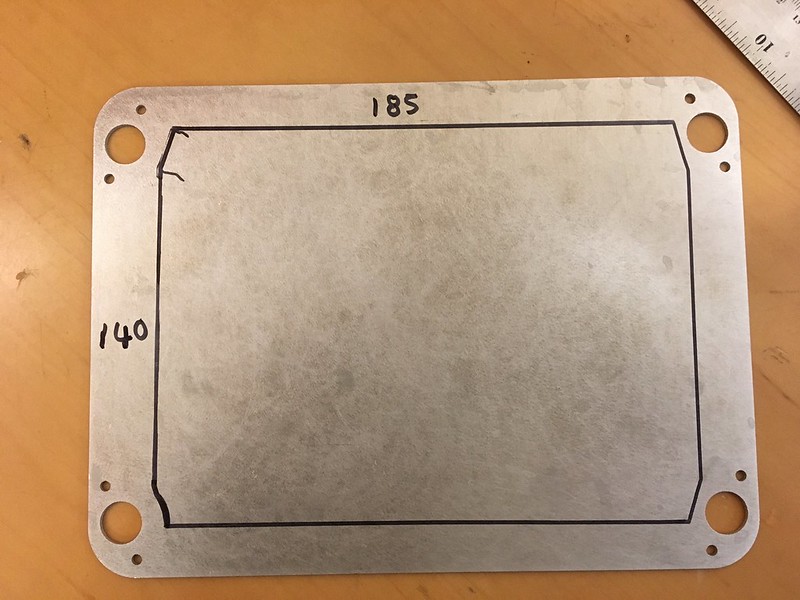
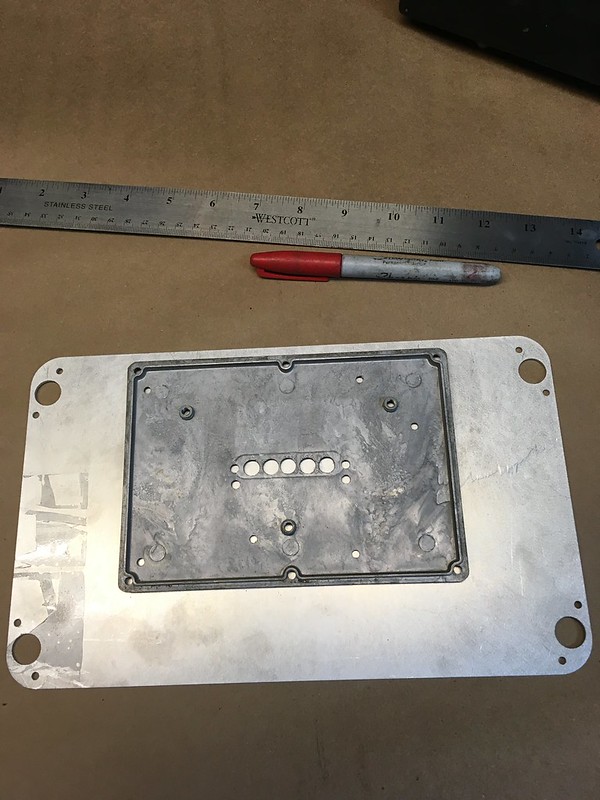
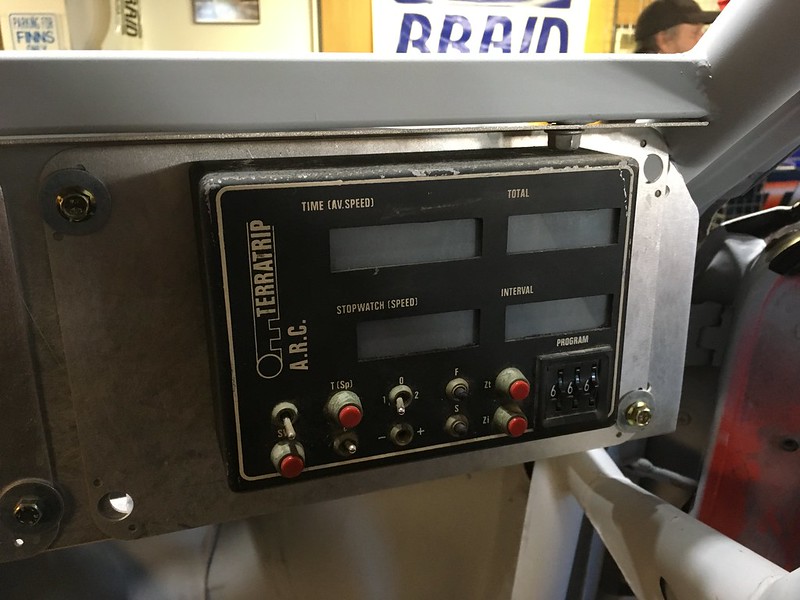
Then we thought we'd have some fun.

We just need to repaint one of the 911s and get a Rothmans Quattro model (on order) and we'll have a perfect set!
FUEL TANK
While we seem to be working on the rear of the car we thought we'd throw in the fuel tank. It's big and takes up a lot of space on the parts shelf. What more rationalization do you need. Oh, we also want to see where the fuels lines exit the trunk area so we can figure out where to locate lines, pumps and filters etc.
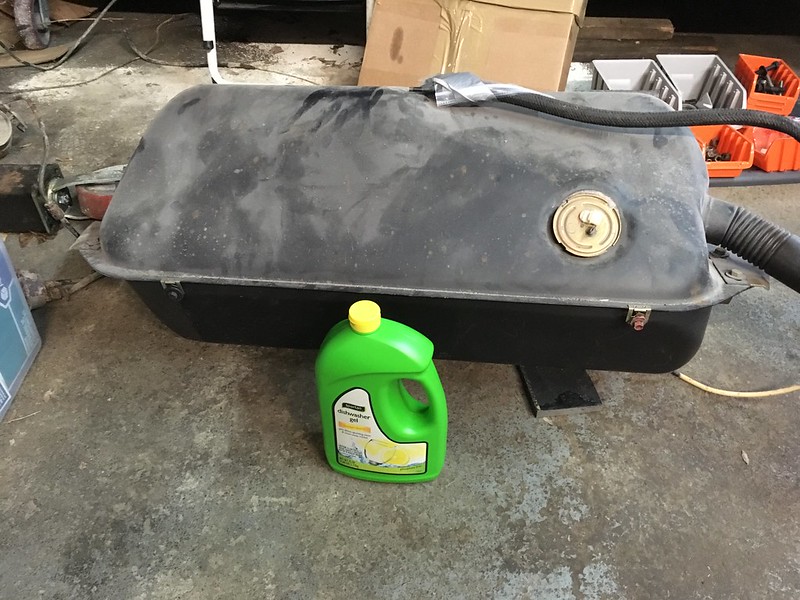
It was a bit awkward to wrestle into location, but soon cooperated.

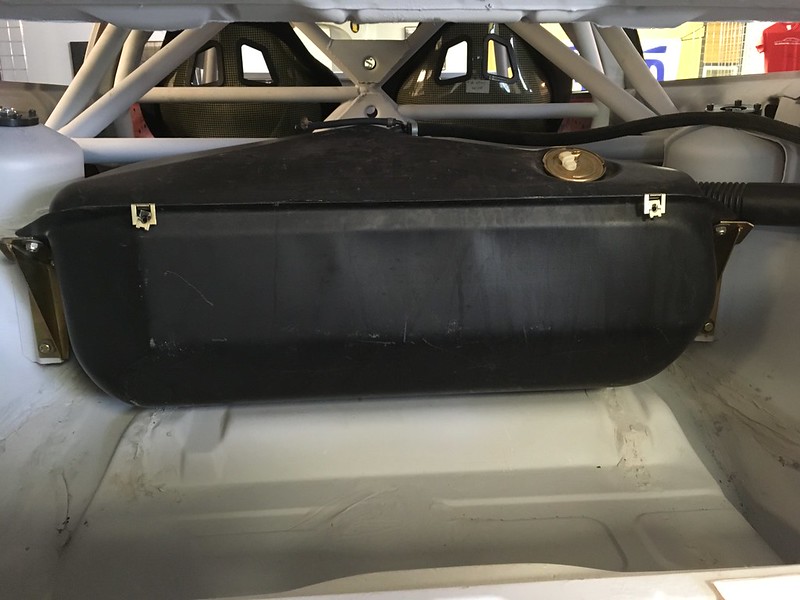

The fuel lines protrude through the trunk floor. Perhaps we can extended them through the lower rear bulkhead and mount the fuel pump/s in the cabin.